Home » Crusher Wear Parts
Myway: Cone & Gyratory Crusher Wear Parts Expert in China
Equipped with advanced automated production lines, Myway crusher wear is engineered for high-wear environments, ensuring the stable and efficient operation of core equipment in your mining, construction and other industries.
- Long wear resistance life
- Metso/Sandvik Compatible
- 7-Day Shipping for Stock Items
- 30% Lower Cost Than OEM Parts
- Having passed ISO9001 certification
Introduction of Crusher Wear Parts
As a main vulnerable part of cone crusher, gyratory crusher and jaw crusher, the bushings bear the core function of reducing friction and supporting the movement of key components. Their performance directly affects the stability, wear life and maintenance cost of crushers.
Myway has been deeply engaged in the field of industrial wear-resistant parts, focusing on the production of wear parts of various crushers including primary gyratory crusher parts, cone crusher spare parts, etc. for more than 20 years.
Using high-quality copper alloy as raw material, the wear life and impact load resistance of Myway crush wear parts are significantly improved, with a service life of up to 15,000 hours.
Its products are widely compatible with international mainstream brand equipment such as Metso HP/GP series, Symons, Gyradisc, etc., providing cost-effective wear-resistant solutions for global mining, sand and gravel aggregates and other industries.
Single Cylinder Series of Crusher Bushings
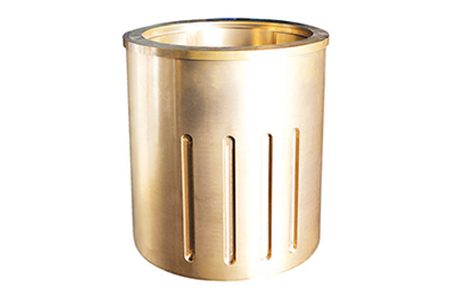
Eccentric Bushing
High-strength bronze for wear resistance and long life. Suitable for high-load, high-temp & corrosive environments. Controllable crushing chamber discharge particle size by adjusting the position of bushing.
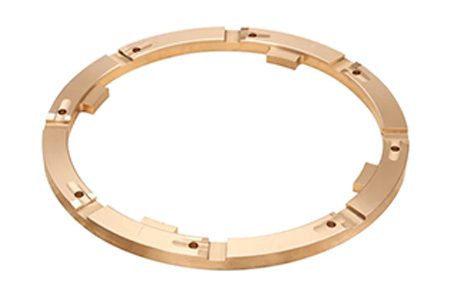
Eccentric Wearing Plate
The arc structure evenly transmits the crushing force to the main frame. Protecting the core components inside the system, like eccentric bushings or spindles. Stable motion trajectory ensures high crushing efficiency.
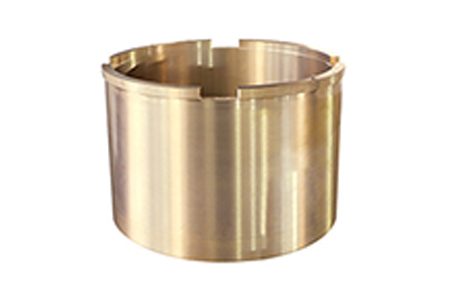
Bottom Shell Bushing
Supporting spindle or bushing to ensure smooth operation. Preventing radial displacement of parts from causing vibration or wear. Dispersing impact force in process of fragmentation, avoiding shell cracking.
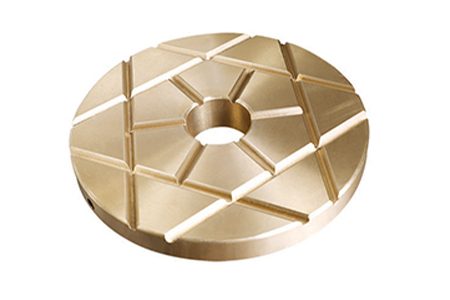
Main Shaft Step
Ensuring the power transmission and structural stability of cone crusher. The stepped geometry provides a precise installation reference. Optimizing the transition corner design to reduce stress concentration.
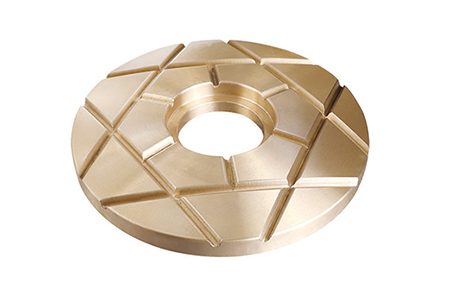
Piston Wearing Plate
Maintaining the sealing and stability of the hydraulic system. Absorbing shock and vibration to reduce system fluctuation. Preventing hydraulic oil leakage and block external dust into the hydraulic chamber.
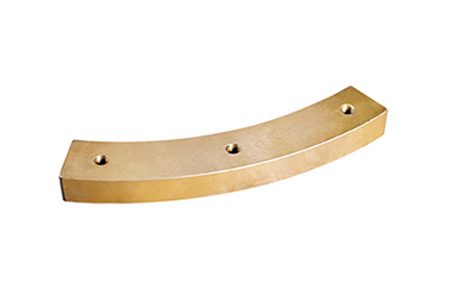
Locating Bar
Connecting the ring and mainframe and fixing position of them. Modular design, can be replaced separately, reduce maintenance costs. Ensuring the accuracy and repeatability of particle size adjustment.
Spring Series of Crusher Wear Parts
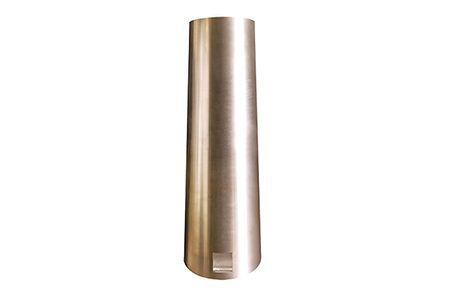
Main Shaft Bushing
High load capacity to withstand lateral loads on the crusher spindle. Integrated axial guide oil groove, combined with pressure lubrication. Shock absorption reduces vibration and noise and improves overall performance.
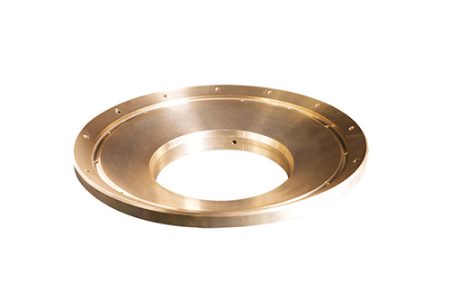
Socket Liner
Connects the main shaft and frame of crusher to optimize load transfer. Avoiding direct friction between parts and avoid wear on the spindle or housing. Reducing the risk of local stress concentration.
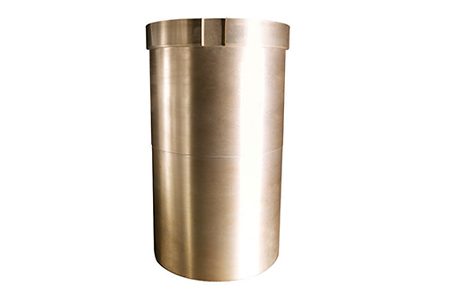
Frame Bushing
Connect the main frame and moving parts of the cone crusher. Precision casting process to ensure the efficient operation of crusher. Suitable for 4.25FT,5.5FT, 7FT mining machines, also support customization.
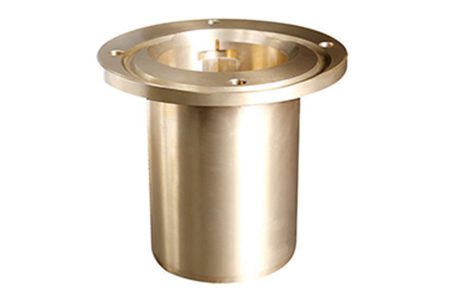
Drive Bushing
Maintain the stability of the drive shaft at high speed. Reducing friction and prolong service life by using oil film or grease film as lubricant. Transmitting the torque of motor or hydraulic motor to eccentric assembly.
Features of Crusher Wear Parts

Wear Resistance
Casting by high-strength aluminum bronze alloy, the wear life of Myway crusher bushing is extremely long, significantly reducing downtime maintenance costs.

Simple Operation
The snap-on/bolt quick-release connection method greatly shortens the replacement time. Its built-in oil tank design also reduces the frequency of lubrication.

High Adaptability
Benefits from corrosion resistance, impact resistance and production sustainability, Myway bushings can be accurately adapted to various models such as cone or gyratory crushers.

One-stop Solution
With experienced team, we can provide you with a full range of services from the selection of crusher wear parts to installation, maintenance, etc.

Quick Delivery
We have 5 distribution centers around the world and have cooperated with DHL/FedEx/UPS/TNT, you can receive the goods within 2 weeks.

Customizable
Myway supports non-standard customization, adapting to the transformation of old equipment and avoiding the replacement of the entire machine.
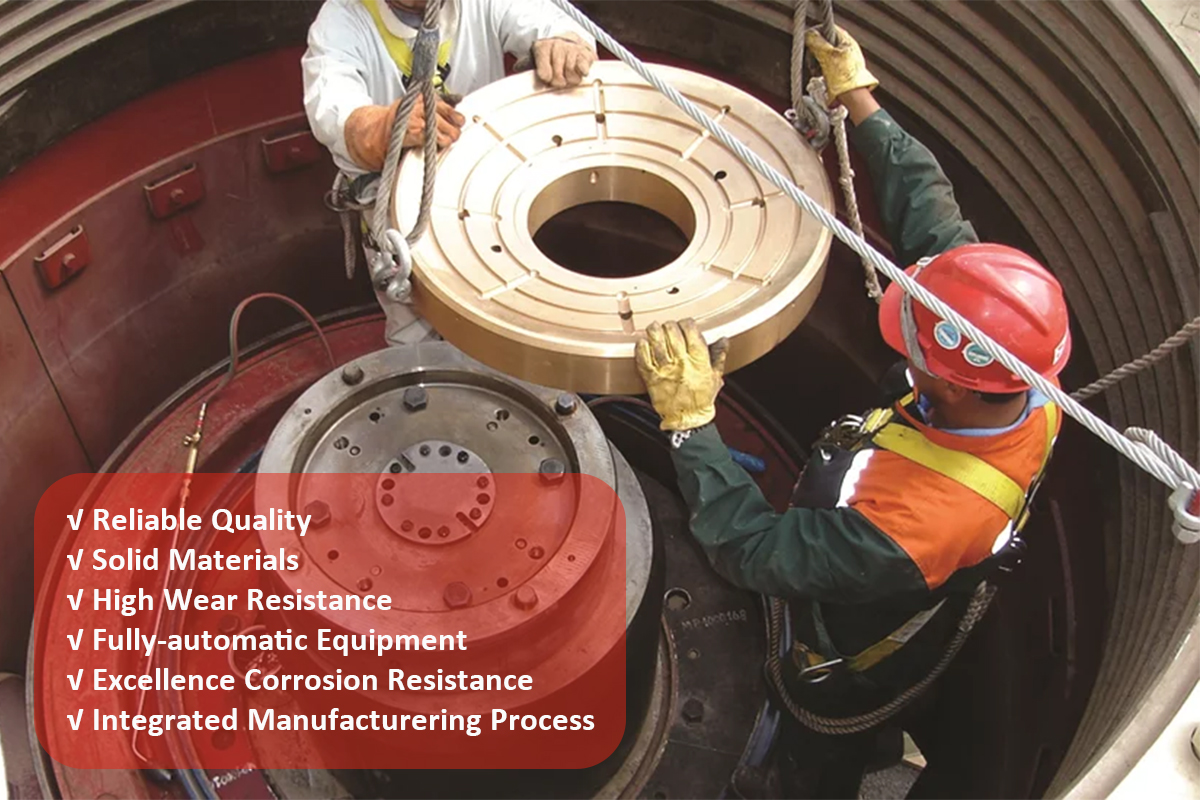
Advantages of
Myway Crusher Wear Parts
- Reliable quality due to the complete product inspection reports
- Solid copper alloy improves compressive strength and provides stable support
- Fully automatic production equipment, professional technology and quality inspection team
- Integrated manufacturing process, from design, production, testing to packaging and delivery
- High wear resistance makes it suitable for high-load scenarios like mining and metallurgy
- Excellent corrosion resistance, performing well in acid or alkaline environment
- Suitable wear shape improves the performance of the crusher and extends the wear life
- Complete types are compatible with the specifications and standards of various crushers
- Comply with OEM standards to ensure the efficiency and safety of the production process
The surface hardness of bushing reaches HB200 and the friction coefficient is 20% lower than that of ordinary bronze
Myway Custom Crusher Wear Parts
Myway specializes in providing tailor-made bushing solutions, offering premium materials such as tin bronze, aluminum bronze, and lead bronze, carefully selected based on the severity of your operational conditions. Our products are designed to meet the rigorous demands of diverse industries, including mining, metallurgy, chemical processing, and construction.
Simply share your requirements with us, and our expertise ensures we can complete design drawings within 3 days, deliver samples within 7 days, and provide complimentary wear testing, spectral analysis, hardness testing, and other inspection reports.
As an original manufacturer of bushings, Myway holds a significant pricing advantage. Our customized solutions offer a 15%-25% cost reduction compared to similar competitors, ensuring you access high-performance products at competitive prices.
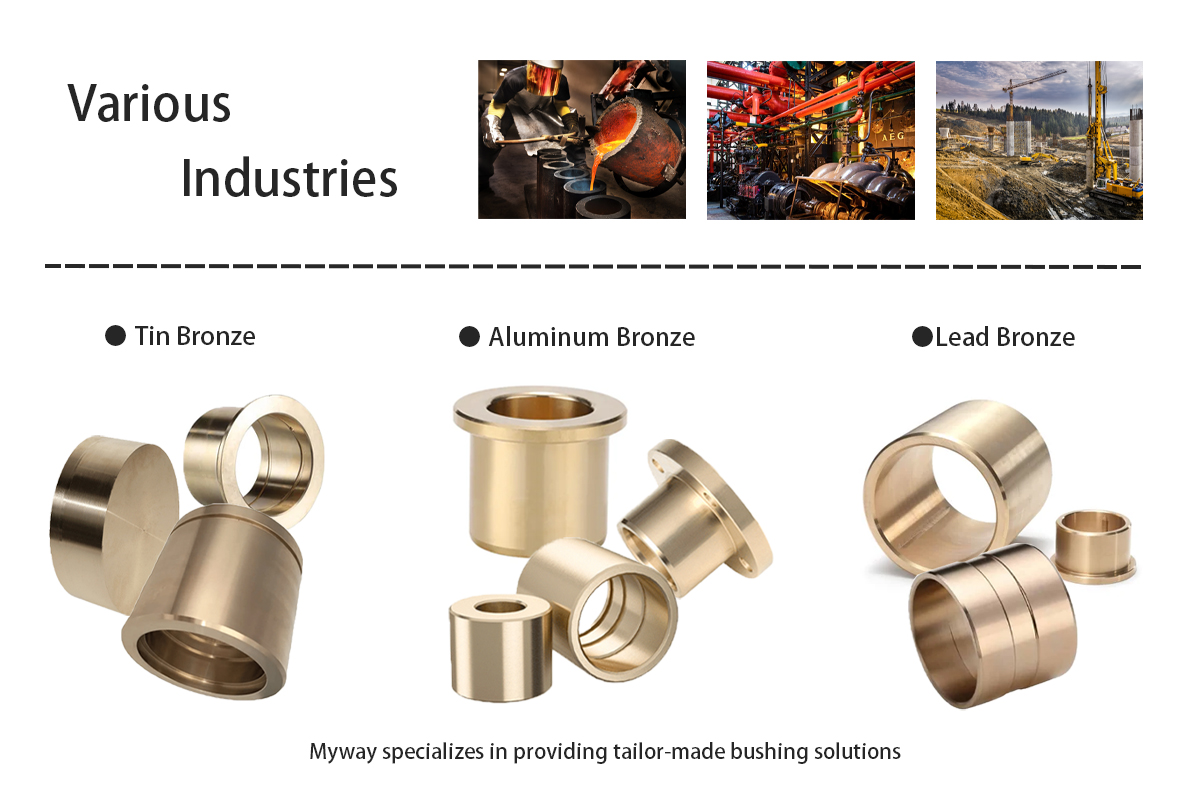
Myway: Your Trustworthy Crusher Wear Parts Manufacturer
FAQs
What Factors Affect the Lifespan of Crusher Wear Parts?
The life of Crusher Wear Parts depends mainly on material properties (like hardness, silicon content), equipment conditions (operating time, load intensity) and material selection.
In addition, regular maintenance (like adjusting equipment clearance, cleaning and lubrication) can extend the service life by 20%-30%, while frequent overloading or high material humidity will accelerate wear.
How to Ensure Crusher Wear Parts Compatibility with Existing Crusher Models?
If you can provide the model, part number or physical drawing of your equipment, Myway can provide products that fully meet your needs.
We can produce replacement bushings for a full range of crusher models, including cone, gyratory, etc., and support customization of various materials and sizes.
What’s the Difference between Manganese Steel and High-chromium Cast Iron Crusher Wear Parts?
High manganese steel (such as ZGMn13Cr2) has high impact toughness and is suitable for processing large hard materials (such as granite). Its surface will harden to above HB550 under impact, and its wear resistance will increase with time.
High chromium cast iron (such as Cr28) is known for its high hardness (HRC≥58) and is suitable for fine crushing of highly abrasive materials (such as quartz sand). Its service life is 3-5 times higher than that of high manganese steel, but it is more brittle.
You can make a comprehensive assessment based on material characteristics, equipment type and budget before making a choice.
How to Control the Maintenance Cost of Crusher Wear Parts?
You need to start with material optimization and preventive maintenance.
For example, the use of high-chromium cast iron hammer heads can reduce the frequency of replacement. Although the single purchase cost is high, the overall cost is reduced by more than 40%.
Regularly check the degree of wear of accessories and adjust equipment parameters in time to avoid downtime losses caused by excessive wear.
How to Install Crusher Wear Parts Correctly to Avoid Failures?
You need to clean the contact surface of the equipment before installation to ensure that there is no debris or rust that affects the fit. You can also choose to have the supplier provide on-site installation guidance or video tutorials to avoid damage to accessories due to improper operation. After installation, a dynamic balance test is required to ensure the stability of the equipment operation.
What are the Key Considerations for International Shipping of Crusher Wear Parts?
For international transportation, you need to choose the appropriate logistics plan according to the weight of the goods and the destination. Small parts can be shipped by air (3-5 days to Europe and the United States), and large equipment is recommended to be shipped by sea (20-30 days) or China-Europe Express (15-20 days).
In order to prevent wear-resistant parts from collision or rust during transportation, we will use wooden frames + anti-rust coating packaging.
What After-sales Services are Included for Crusher Wear Parts?vice
Myway adjusts the material, size or surface treatment process of accessories according to customer needs. Our sales provide you with 7×24 hours online consulting service, providing accessories selection, installation and debugging and troubleshooting guidance.
If you want to establish long-term cooperative relationship with us, of course there will be a bigger discount.
Sandvik OEM Model Table
OEM Number | Model | Description |
---|---|---|
442.6131-01 | CS420 | Bottom shell bushing |
422.6143-01 | CS420 | Locating Bar |
442.9686-01 | CS420 | Eccentric bushing |
442.9688-01 | CS420 | Eccentric bushing |
442.6139-01 | CS420 | Piston wearing plate |
442.6138-01 | CS420 | Main shaft step |
442.6996-01 | CS420 | Eccentric bushing |
452.4190-001 | CS430 | Bottom Shell Bushing |
452.4516-001 | CS430 | Eccentric bushing 16+20+25+30 |
442.7893-01 | CS430 | Piston wearing plate |
442.7895-01 | CS430 | Mainshaft step |
442.8486-01 | CS430 | Eccentric bushing,16/20/25/30 |
442.7122-01 | CS440 | Piston wearing plate |
442.7120-01 | CS440 | Mainshaft step Pt. |
442.7146-01 | CS440 | Bottom shell bushing |
442.7107-01 | CS440 | Eccentric wearing plate |
442.8067-01 | CS440 | Eccentric bushing 20, 25, 30, 36, no keyway 442.6-01 |
452.7275-001 | CS550 | Eccentric wearing plate |
452.7275-001 | CS550 | Eccentric wearing plate CH550 |
452.7276-001 | CS550 | Bottom shell bushing |
452.7275-001 | CS550 | Eccentric wearing plate |
442.8742-01 | CS660 | Bottom shell bushing |
442.9033-01 | CS660 | Eccentric bushing |
442.8761-01 | CS660 | Ecc. wearing plate |
442.8730-01 | CS660 | Piston wearing plate |
442.8732-01 | CS660 | Main shaft step |
BG01074558 | CS840i | Bottom shell bushing |
BG01074558 | CS840i | Bottom shell bushing |
BG01074558 | CS840i | Bottom shell bushing |
442.9657-01 | CH420 | Eccentric bushing 13+16+18, machinning 442.6995 |
442.9658-01 | CH420 | Eccentric bushing 18+20+22 |
442.9659-01 | CH420 | Eccentric bushing 22+25+28 |
442.6139-01 | CH420 | Piston wearing plate |
442.6138-01 | CH420 | Main shaft step |
442.6131-01 | CH420 | BOTTOMSHELL BUSHING /H2000, N11851103 |
442.9686-01 N11851670 | CH420 | ECCENTRIC BUSHING 13+16+20+25 /S2800 |
442.9659-01 N11851664 | CH420 | ECCENTRIC BUSHING 22+25+28 /H2000 |
442.9658-01 N11851663 | CH420 | ECCENTRIC BUSHING 18+20+22 /H2000 |
442.9657-01 N11851662 | CH420 | ECCENTRIC BUSHING 13+16+18 /H2000 |
442.6130-01 | CH420 | ECCENTRIC WEARING PLATE H/S2000, N11851102 |
442.6139-01 N11851109 | CH420 | PISTON WEARING PLATE |
442.6138-01 N11851108 | CH420 | MAIN SHAFT STEP |
452.4190-001 | CH430 | Bottom Shell Bushing |
452.4191-01 | CH430 | Eccentric bushing 16+19+22 |
452.4192-001 | CH430 | Eccentric bushing 22+25+29 |
452.4193-01 | CH430 | Eccentric bushing 29+32+34+36,blank 452.4189-001 |
442.7928-01 | CH430 | Locating Bar |
442.7893-01 | CH430 | Piston wearing plate |
442.7895-01 | CH430 | Main shaft step |
442.7927-01 | CH430 | Eccentric wear plate |
442.7925-01 | CH430 | Eccentric bushing,29+32+34+36 |
442.7935-01 | CH430 | BOTTOM SHELL BUSHING |
442.7924-01 | CH430 | Eccentric bushing,22+25+29 |
442.7935-01 | CH430 | BOTTOM SHELL BUSHING, N11851322 |
442.8486-01/452.4516-001 N11851409 | CH430 | ECCENTRIC BUSHING 16+20+25+30/ |
452.4193-001 | CH430 | ECCENTRIC BUSHING 29 32 34 36,blank 442.7922, N11851309, 442.7925-01 |
442.7924-01/452.4192-001 N11851308 | CH430 | ECCENTRIC BUSHING 22+25+29 |
442.7923-01/452.4191-001 N11851307 | CH430 | ECCENTRIC BUSHING 16+19+22 |
452.4188-001 | CH430 | ECCENTRIC WEARING PLATE, 442.7927-01, N11851311 |
442.7893-01 | CH430 | PISTON WEARING PLATE, N11851295 |
442.7895-01 | CH430 | MAIN SHAFT STEP, N11851297 |
452.1954-902 | CH430 | CONCAVE RING LOWER C STEPPED 2 18MNCR CS430, MM1328141 |
442.7146-01 | CH440 | Bottom shell bushing |
442.9643-01 | CH440 | Eccentric bushing 13+16+20+24,without keyway 442.9404 |
442.9642-01 | CH440 | Eccentric bushing 24 28 32 |
442.9406-01 | CH440 | Eccentric bushing 32+36+40+44 |
442.7107-01 | CH440 | Eccentric wearing plate |
442.7110-01 | CH440 | Locating Bar |
442.7122-01 | CH440 | Piston wearing plate |
442.7120-01 | CH440 | Main shaft step |
442.7146-01 | CH440 | BTTMSHELL BUSHING H/, N11851199 |
442.9643-01 | CH440 | ECCENTRIC BUSHING 13+16+20+24 //CH440, N11851661 |
442.9642-01 | CH440 | ECCENTRIC BUSHING 24+28+32 / /CH440, N11851660 |
442.9406-01 | CH440 | ECCENTRIC BUSHING 32+36+40+44 //CH440, N11851617 |
442.7107-01 | CH440 | ECCENTRIC WEARING PLATE H/, N11851179 |
442.7122-01 | CH440 | PISTON WEARING PLATE, N11851187 |
442.7120-01 N11851185 | CH440 | MAIN SHAFT STEP |
BG00203559 | CH540 | Bottom shell bushing |
BG00203559 | CH540 | Bottom shell bushing |
BG00203559 | CH540 | Bottom shell bushing |
BG01074558 | CH550 | Bottom shell bushing |
442.8742-01 | CH660 | Bottom shell bushing Casquillo de chasis Douille de bâtie,R 223.1117,11 |
442.8824-01 | CH660 | Eccentric bushing,18+20+24+28,R 223.1117,11 |
442.8825-01 | CH660 | Eccentric bushing,28+32+36+40,R 223.1117,11 |
442.8826-01 | CH660 | Eccentric bushing,40+44+48+50 Casquillo de excéntrica,R 223.1117,11 |
442.8761-02 | CH660 | Ecc. wearing plate Arandela de cojinete Rondelle de palier,R 223.1117,11 |
442.8762-01 | CH660 | Locating Bar |
442.8730-01 | CH660 | Piston wearing plate,R 223.1117,11 |
442.8732-01 | CH660 | Main shaft step Placa de presion Plaque de pression,R 223.1117,11 |
442.8742-01 | CH660 | Bushing - bottom shell Casquillo de bastidor Douille de bâti |
442.8824-01 | CH660 | Eccentric bushing,18+20+24+28 Casquillo de excéntrica,Douille d'excentrique |
442.8825-01 | CH660 | Eccentric bushing,28+32+36+40 Casquillo de excéntrica,Douille d'excentrique |
442.8826-01 | CH660 | Eccentric bushing,40+44+48+50 Casquillo de excéntrica,Douille d'excentrique |
442.8761-02 | CH660 | Wearing plate Arandela de cojinete Rondelle de palier |
442.8730-01 | CH660 | Piston wearing plate Placa de presion Plaque de pression |
442.8732-01 | CH660 | Main shaft step,Placa de presion, superior Plaque de pression supérieure |
442.8742-01 | CH660 | BOTTOMSHELL BUSHING H/, N11851439 |
442.9033-01 N11851516 | CH660 | ECCENTRIC BUSHING 20+25+30+35+40 //CS660 |
442.8826-01 | CH660 | ECCENTRIC BUSHING 40+44+48+50 /, N11851488 |
442.8825-01 N11851487 | CH660 | ECCENTRIC BUSHING 28+32+36+40 / |
442.8824-01 N11851486 | CH660 | ECCENTRIC BUSHING 18+20+24+28 / |
442.8761-01 | CH660 | ECCENTRIC WEARING PLATE H/, N11851446 |
442.8730-01 N11851433 | CH660 | PISTON WEARING PLATE |
442.8732-01 N11851435 | CH660 | MAIN SHAFT STEP |
BG01086428 | CH830i | Bottom shell bushing |
BG01074558 | CH840i | Bottom shell bushing |
BG01074558 | CH840i | Bottom shell bushing |
BG01074558 | CH840i | Bottom shell bushing |
452.7644-001 | CH860i | Bottomshell bushing JM 14-15 |
452.7644-001 | CH860i | Bottom shell bushing |
452.7644-001 | CH865i | Bottomshell bushing JM 14-15 |
452.7644-001 | CH865i | Bottom shell bushing |
452.0834-001 | CH870 | Locating Bar |
452.0805-001 | CH870 | Eccentric bushing, throw 32-37-42-47 |
452.0806-901 | CH870 | Eccentric bushing, throw 47-52-57-62 |
452.0807-901 | CH870 | Eccentric bushing, throw 62-68-74-80,blank 452.0803 |
452.0805-001 | CH870 | Eccentric bushing, throw 32-37-42-47 |
452.0795-001 | CH870 | Bottom shell bushing |
452.0808-001 | CH870 | Eccentric wearing plate |
452.0795-001 | CH870 | Bottom shell bushing |
452.0805-001 | CH870 | Eccentric bushing 32+37+42+47,Alternative or order connected. |
452.0806-001 | CH870 | Eccentric bushing 47+52+57+62 |
452.0807-001 | CH870 | Eccentric bushing 62+68+74+80 |
452.0808-001 | CH870 | Eccentric wearing plate |
452.0795-001 N11852081 | CH870 | BOTTOM SHELL BUSHING |
452.0805-001 N11852086 | CH870 | ECCENTRIC BUSHING 32+37+42+47 |
452.0806-001 N11852085 | CH870 | ECCENTRIC BUSHING 47+52+57+62 |
452.0807-001 N11852084 | CH870 | ECCENTRIC BUSHING 62+68+74+80 |
452.0808-001 | CH870 | ECCENTRIC WEARING PLATE, N11852087 |
452.0507-001 | CH870 | Main shaft step |
452.0538-01 | CH870 | Piston wearing plate |
452.0805-001 | CH870i | Eccentric bushing, throw 32-37-42-47 |
452.0806-901 | CH870i | Eccentric bushing, throw 47-52-57-62 |
452.0807-901 | CH870i | Eccentric bushing, throw 62-68-74-80 |
452.0805-001 | CH870i | Eccentric bushing, throw 32-37-42-47 |
452.0795-001 | CH870i | Bottom shell bushing |
452.0808-001 | CH870i | Eccentric wearing plate |
452.0795-001 | CH870i | Bottom shell bushing |
452.0805-001 | CH870i | Eccentric bushing 32+37+42+47,Alternative or order connected. |
452.0806-001 | CH870i | Eccentric bushing 47+52+57+62 |
452.0807-001 | CH870i | Eccentric bushing 62+68+74+80 |
452.0808-001 | CH870i | Eccentric wearing plate |
442.9248-01 | CH880 | Bottomshell bushing,See chapter 11 |
442.9308-01 | CH880 | Locating Bar |
442.9724-01 | CH880 | Piston wearing plate |
442.9248-01 | CH880 | Bottomshell bushing Casquillo de bastidor Douille de bâti |
442.9724-01 | CH880 | Piston wearing plate Placa de presión, inferior Grain porteur |
442.9248-01 N11851550 | CH880 | BOTTOM SHELL BUSHING |
442.9724-01 N11851673 | CH880 | PISTON WEARING PLATE |
442.9248-01 | CH890 | Bottomshell bushing |
442.9248-01 N11851550 | CH890 | BOTTOM SHELL BUSHING |
442.9248-01 | CH890i | Bottom shell bushing |
442.9248-01 | CH890i | Bottom shell bushing |
442.9248-01 | CH895i | Bottom shell bushing |
442.9248-01 | CH895i | Bottom shell bushing |
442.9871-901 | H2800 | BOTTOM SHELL ASM |
442.6174-01 | H2800 | PINSHFT ARM LINER |
442.6175-01 | H2800 | NARROW ARM LINER |
442.6131-01 | H2800 | BOTTOM SHELL BUSH |
442.6132-01 | H2800 | DUST COLLAR |
442.6216-01 | H2800 | GASKET |
442.6146-01 | H2800 | INR DUST SEAL RING |
899.0229-00 | H2800 | PROTECTIVE CAP SW55 2 G60SVART |
442.6183-01 | H2800 | ECCENTRIC |
442.9657-01 | H2800 | ECC BUSH 13+16+18 |
442.9658-01 | H2800 | ECC BUSH 18+20+22 |
442.9659-01 | H2800 | ECC BUSH 22+25+28 |
442.6152-01 | H2800 | HUB S2800 |
442.6127-00 | H2800 | GEAR & PINION SET SPIRAL BEV |
442.6130-01 | H2800 | WEARING PLATE |
853.0619-00 | H2800 | SPRING PIN PRYM 12 X 40 |
442.9872-01 | H2800 | HYDROSET CYLINER |
442.9873-01 | H2800 | HYDROSET CYL BUSH |
442.9655-00 | H2800 | PISTON H/S-2800 |
442.6139-01 | H2800 | PISTON WRG PLATE |
442.6137-01 | H2800 | STEP WASHER |
442.6153-00 | H2800 | CHEVRON PACKING |
442.6179-01 | H2800 | PACKING CLAMP PLT |
442.8783-01 | H2800 | COVER PLATE CLOSURE PLUG |
984.0391-00 | H2800 | TRANSDUCER PROBE |
442.6627-901 | H2800 | PINIONSHAFT ASM. |
442.6134-01 | H2800 | PINIONSHAFT HOUSING |
868.0801-00 | H2800 | SPHERICAL ROLLER BEARING |
868.0801-00 | H2800 | SPHERICAL ROLLER BEARING |
442.6148-01 | H2800 | SPACER |
442.6148-01 | H2800 | SPACER |
873.1012-00 | H2800 | OIL SEAL RING |
900.0717-00 | H2800 | FILTER PLUG |
442.6202-01 | H2800 | PINSHAFT HSG PLUG |
442.6133-01 | H2800 | PINIONSHAFT |
857.0051-00 | H2800 | KEY R 18X11X70 |
900.0269-00 | H2800 | NIPPLE RSK 124 16 45 |
900.0275-00 | H2800 | SLEEVE 3/4" RSK |
442.7591-901 | H2800 | MAINSHAFT SLV & DWL |
442.7450-01 | H2800 | MAINSHAFT |
442.6140-01 | H2800 | MAINSHAFT SLEEVE |
853.0645-00 | H2800 | PARALLEL PIN M16X40 |
442.6138-01 | H2800 | MAINSHAFT STEP |
442.7449-01 | H2800 | HEADCENTER |
442.7000-01 | H2800 | MANTLE EF M1 |
442.7000-02 | H2800 | MANTLE EF M2 |
442.9698-01 | H2800 | MANTLE A M1 |
442.9698-02 | H2800 | MANTLE A M2 |
442.6197-01 | H2800 | MANTLE B M1 |
442.6197-02 | H2800 | MANTLE B M2 |
442.9761-01 | H2800 | MANTLE HC M1 |
442.9761-02 | H2800 | MANTLE HC M2 |
442.6194-00 | H2800 | HEADNUT W/BURNING RING |
442.6193-01 | H2800 | INNER HEAD NUT |
442.6217-01 | H2800 | BURNING RING |
442.6906-01 | H2800 | DUST SEAL RING |
442.6932-01 | H2800 | SCRAPER |
442.9674-901 | H2800 | TOP SHELL ASM |
442.9568-01 | H2800 | SPIDER ARM SHIELD |
442.8362-01 | H2800 | SPIDER CAP |
873.0831-00 | H2800 | O-RING |
442.8363-01 | H2800 | SPIDER BUSHING |
442.8364-01 | H2800 | SPIDER BUSHING OIL SEAL |
442.9583-01 | H2800 | CONCAVE RNG EF M1 |
442.9583-02 | H2800 | CONCAVE RNG EF M2 |
442.9584-01 | H2800 | CONCAVE RING F M1 |
442.9584-02 | H2800 | CONCAVE RING F M2 |
442.9585-01 | H2800 | CONCAVE RING MF M1 |
442.9585-02 | H2800 | CONCAVE RING MF M2 |
442.9586-01 | H2800 | CONCAVE RING M M1 |
442.9586-02 | H2800 | CONCAVE RING M M2 |
442.9587-01 | H2800 | CONCAVE RING C M1 |
442.9587-02 | H2800 | CONCAVE RING C M2 |
442.9569-01 | H2800 | CONCAVE RING EC M1 |
442.9569-02 | H2800 | CONCAVE RNG EC M1 |
442.9596-01 | H2800 | FILLER RING C(EF, F, MF, M) |
840.1093-00 | H2800 | SCREW M65 20X280 8.8 |
845.0203-00 | H2800 | LOCKNUT M20 8 |
442.9572-01 | H2800 | SLEEVE |
442.9573-01 | H2800 | WASHER |
863.0065-00 | H2800 | DISC SPRING |
442.1843-00 | H2800 | OIL SCREEN |
442.6614-00 A | H2800 | LUBE PUMPING UNIT |
906.0140-00 | H2800 | OIL PUMP |
906.0339-00 | H2800 | COMPLETE MOUNTING SET |
910.0101-00 | H2800 | AIR-OIL COOLER |
910.0111-00 | H2800 | FAN WHEEL 60HZ |
972.0359-00 | H2800 | MOTOR MT90L-4 3601 380/420VY |
912.0096-00 | H2800 | DIRT TRAP SW/0 1 1/4" 0,6MM 740010 |
902.0717-00 | H2800 | RELIEF VALVE R1 3880901 |
984.1008-00 | H2800 | LIQUID LEVEL SWITCH |
442.6956-00 A | H2800 | HYDROSET PUMP UNIT |
919.0163-00 | H2800 | ACCUMULATOR 10L |
919.0173-00 | H2800 | VALVE/PORT ASM |
442.8624-00 | H2800 | CHECK VALVE |
127.0004-30 | H2800 | CHECK VALVE SPRING |
984.0607-00 | H2800 | IMMERSION HEATER 1640W |
442.6644-01 | H2800 | FIXING PLATE LOWER |
442.6643-00 | H2800 | TOP PLATE COMP MTG |
864.0070-00 | H2800 | RUBBER COMPRESSION MOUNT |
442.7908-00 | H3800 | BOTTOM SHELL ASM |
442.7915-01 | H3801 | PINSHFT ARM LINER |
442.7914-01 | H3802 | NARROW ARM LINER |
442.7935-01 | H3803 | BOTTOM SHELL BUSH |
442.7929-01 | H3804 | DUST COLLAR |
442.7934-01 | H3805 | GASKET |
442.7931-01 | H3806 | INR DUST SEAL RING |
899.0229-00 | H3807 | PROTECTIVE CAP SW55 2 H20SVART |
442.7921-01 | H3808 | ECCENTRIC |
442.7923-01 | H3809 | ECC BUSH 16+19+22 |
442.7924-01 | H3810 | ECC BUSH 22+25+29 |
442.7925-01 | H3811 | ECC BUSH 29+32+34+36 |
442.7926-01 | H3812 | HUB |
442.7802-00 | H3813 | GEAR & PINION SET SPIRAL BEV |
442.7927-01 | H3814 | WEARING PLATE |
853.0474-00 | H3815 | PIN PRYM 12 X 45 |
442.7889-01 | H3816 | HYDROSET CYLINER |
442.7892-01 | H3817 | HYDROSET CYL BUSH |
442.9668-00 | H3818 | HYD PISTON ASM |
442.7893-01 | H3819 | PISTON WRG PLATE |
442.7894-01 | H3820 | STEP WASHER |
442.7897-00 | H3821 | CHEVRON PACKING |
442.7896-01 | H3822 | PACKING CLAMP PLT |
442.8783-01 | H3823 | COVER PLATE CLOSURE PLUG |
984.0391-00 | H3824 | TRANSDUCER PROBE H/ 4800 *NOTE* |
819.0061-00 | H3825 | PROTECTIVE HOSE SEE 819.0061 |
442.7559-01 | H3826 | MEASURING TUBE ,4000 |
442.7949-01 | H3827 | PINIONSHAFT HOUSING |
00-813-250-030 | H3828 | SPHERICAL ROLLER BEARING |
00-813-255-031 | H3829 | SPHERICAL ROLLER BEARING |
442.7954-01 | H3830 | SPACER |
873.1097-00 | H3831 | OIL SEAL RING CC OIL SEAL R |
900.0717-00 | H3832 | VENT FITTING 1/4 F14 |
442.7959-01 | H3833 | PINSHAFT HSG PLUG |
442.9936-01 | H3834 | PINIONSHAFT |
857.0046-00 | H3835 | KEY R 16X10X80 |
900.0269-00 | H3836 | NIPPLE RSK 124 16 45 DN 20 |
900.0275-00 | H3837 | SLEEVE 3/4" RSK 1058 |
442.8923-AD | H3838 | MAINSHAFT SLV & DWL |
442.7902-01 | H3839 | MAINSHAFT |
442.7913-01 | H3840 | MAINSHAFT SLEEVE |
853.0118-00 | H3841 | PARALLEL PIN H-36 M25X50 |
442.7895-01 | H3842 | MAINSHAFT STEP |
442.7910-01 | H3843 | HEADCENTER |
442.7988-01 | H3844 | MANTLE A M1 |
442.7988-02 | H3845 | MANTLE A M2 |
442.7989-01 | H3846 | MANTLE B M1 |
442.7989-02 | H3847 | MANTLE B M2 |
442.8629-01 | H3848 | MANTLE EF M1 |
442.8629-02 | H3849 | MANTLE EF M2 |
442.7912-00 | H3850 | HEADNUT W/BURNING RING |
442.7918-01 | H3851 | INNER HEAD NUT |
442.7911-01 | H3852 | BURNING RING |
442.8017-01 | H3853 | DUST SEAL RING |
442.8022-01 | H3854 | SCRAPER |
442.8314-901 | H3855 | TOP SHELL EC2 |
442.7984-01 | H3856 | SPIDER ARM SHIELD |
442.7976-01 | H3857 | SPIDER CAP |
873.0833-00 | H3858 | O-RING 5.7 x 379.3 x 390.7 |
442.6473-01 | H3859 | SPIDER BUSHING |
442.6470-01 | H3860 | SPIDER BUSHING OIL SEAL |
442.8003-01 | H3861 | CONCAVE RNG MF M1 |
442.8003-02 | H3862 | CONCAVE RNG MF M2 |
442.8246-01 | H3863 | CONCAVE RING M M1 |
442.8246-02 | H3864 | CONCAVE RING M M2 |
442.8247-01 | H3865 | CONCAVE RING MC M1 |
442.8247-02 | H3866 | CONCAVE RING MC M2 |
442.8248-01 | H3867 | CONCAVE RING C M1 |
442.8248-02 | H3868 | CONCAVE RING C M2 |
442.8249-01 | H3869 | CONCAVE RING EC M1 |
442.8249-02 | H3870 | CONCAVE RING EC M2 |
442.8251-01 | H3871 | CONCAVE RING F M1 |
442.8630-01 | H3872 | CONCAVE RNG EF M1 |
442.8008-01 | H3873 | FILLER RING M(F, MF) |
442.8245-01 | H3874 | FILLER RING C(EF,MC) |
442.8001-01 | H3875 | SCREW M65 24X360 8.8 |
442.7996-01 | H3876 | SLEEVE |
847.0264-00 | H3877 | WASHER |
847.0265-00 | H3878 | WASHER |
442.7999-01 | H3879 | LOCATING BAR |
442.7986-90 | H3880 | CONICAL INSERT R.H. (EC) |
442.7986-00 | H3881 | CONICAL INSERT L.H. (EC) |
442.1843-00 | H3882 | OIL SCREEN |
442.3300-90 | H3883 | LUBE PUMPING UNIT |
906.0140-00 | H3884 | OIL PUMP RB5-01V 38-82874 PUMPING UN |
930.0234-00 | H3885 | COUPLING HALF D25 05-32-116 |
930.0235-00 | H3886 | COUPLING HALF D28 05-32-538 |
442.2873-90 | H3887 | HEAT EXCHANGER 502-0-4BCFH2000 |
910.0055-90 | H3888 | AIR-OIL COOLER 58-650-41-1.5 |
906.0298-00 | H3889 | FAN WHEEL 60HZ FOR MK 001 |
906.0307-00 | H3890 | IMPELLER BLADES-MK.001 |
910.0063-00 | H3891 | RADIATOR UNIT |
972.0359-00 | H3892 | MOTOR MT90L-4 3601 380/420VY |
912.0096-00 | H3893 | DIRT TRAP SW/0 1 1/4" 0,6MM 740010 |
902.0717-00 | H3894 | RELIEF VALVE R1 3880901 |
984.1008-00 | H3895 | LIQUID LEVEL SWITCH |
44-100-083-001 | H3896 | PIPE NIPPLE ADAPTER 3.0 BSP TO |
900.0314-00 | H3897 | SLEEVE |
442.6956-00 | H3898 | HYDROSET PUMP UNIT |
919.0164-00 | H3899 | ACCUMULATOR 20L OLAER |
919.0173-00 | H3900 | VALVE/PORT ASM |
442.8624-00 | H3901 | CHECK VALVE / |
127.0004-30 | H3902 | CHECK VALVE SPRING |
650.0173-02 | H3903 | HYDRAULIC HOSE 2X695+5 |
984.0316-00 | H3904 | IMMERSION HEATER 380V, 670W |
984.0607-00 | H3905 | IMMERSION HEATER 1640W |
442.9780-01 | H3906 | BOTTOM PLT COMP MTG |
442.9779-00 | H3907 | TOP PLATE COMP MTG |
864.0080-00 | H3908 | STAMP "A" RUBBER COMPRESSION MOUNT |
442.9476-00 | H3909 | TOOL BOX S 3000,4000 . |
442.0800-90 | H3910 | LEAD-CHECK OF C.S.S. |
442.8044-01 | H3911 | EYEBOLT-LIFTING PLT |
442.8042-00 | H3912 | LIFTING TOOL-ECC SLV |
920.0109-00 | H3913 | SLUGGING WRENCH |
920.0131-00 | H3914 | COMBINATION WRENCH 46MM |
920.0134-00 | H3915 | COMBINATION WRENCH 30MM |
920.0135-00 | H3916 | COMBINATION WRENCH 36MM |
920.0105-00 | H3917 | U-SPANNER NV 36MM 3000 |
920.0032-00 | H3918 | SOCKET SCREW KEY 5/8" |
920.0035-00 | H3919 | SOCKET SCREW KEY 5 |
920.0036-00 | H3920 | SOCKET SCREW KEY 6 |
920.0037-00 | H3921 | SOCKET SCREW KEY 8 |
920.0038-00 | H3922 | SOCKET SCREW KEY 10 MM |
920.0040-00 | H3923 | SOCKET SCREW KEY 14 |
843.1330-00 | H3924 | STUD BOLT |
442.6566-00 | H3925 | PISTON STOP PLATE |
442.8866-01 | S3800 | BTMSHELL SIDE LINER |
442.8865-01 | S3801 | BTMSHELL SIDE LINER |
442.8868-01 | S3802 | BTMSHELL SIDE LINER |
442.8869-01 | S3803 | BTMSHELL SIDE LINER |
442.8867-01 | S3804 | BTMSHELL SIDE LINER |
442.8864-01 | S3805 | BTMSHELL SIDE LINER |
442.8449-01 | S3806 | ECCENTRIC |
442.8486-01 | S3807 | ECC BUSH 16/20/25/30 |
452.0678-901 | S3808 | MAINSHAFT ASSEMBLY |
452.0651-001 | S3809 | MAINSHAFT |
442.7913-01 | S3810 | MAINSHAFT SLEEVE |
452.0632-001 | S3811 | HEADCENTER |
442.8470-01 | S3812 | MANTLE A M1 |
442.8470-02 | S3813 | MANTLE A M2 |
442.8471-01 | S3814 | MANTLE B M1 |
442.8471-02 | S3815 | MANTLE B M2 |
442.8446-01 | S3816 | TOPSHELL EC2 |
442.9035-01 | S3817 | TOPSHELL LINER |
853.0979-00 | S3818 | DOWEL PIN 36 X 32 |
442.8451-01 | S3819 | ARM SHIELD |
442.8551-01 | S3820 | DOWEL PIN-SPDR ARM SHLD |
442.8520-00 | S3821 | SPIDER CAP |
442.8477-00 | S3822 | LWR CONCAVE EC M1 |
442.8477-90 | S3823 | LWR CONCAVE EC M2 |
442.8478-00 | S3824 | LWR CONCAVE C M1 |
442.8478-90 | S3825 | LWR CONCAVE C M2 |
442.8484-00 | S3826 | UPR CONCAVE EC M1 |
442.8484-90 | S3827 | UPR CONCAVE EC M2 |
442.8485-00 | S3828 | UPR CONCAVE C M1 |
442.8485-90 | S3829 | UPR CONCAVE C M2 |
452.0230-902 | H4800 | BOTTOM SHELL |
442.7201-00 | H4800 | BOTTOM SHELL COVER |
442.7140-00 | H4800 | PINSHAFT ARM LINER |
442.7141-00 | H4800 | NARROW ARM LINER |
442.7146-01 | H4800 | BOTTOM SHELL BUSH |
442.7106-01 | H4800 | DUST COLLAR |
442.7109-01 | H4800 | RING |
442.7110-01 | H4800 | LOCATING BAR |
442.7168-01 | H4800 | SHIM 0.1 THK(0.003) |
442.7168-02 | H4800 | SHIM 0.5 THK(0.02) |
442.7168-03 | H4800 | SHIM 0.7 THK(0.03) |
442.7168-04 | H4800 | SHIM 1.0 THK(0.04) |
442.7170-01 | H4800 | DUST COLLAR GASKET |
442.7108-01 | H4800 | INNER SEAL RING |
923.0351-00 | H4800 | TEMPERATURE TRANSMITTER |
899.0278-00 | H4800 | PROTECTIVE CAP M42 SW65-2-G68 |
442.9530-01 | H4800 | SCREW M6S 42X100 8.8 |
442.7151-01 | H4800 | ECCENTRIC |
442.9406-01 | H4800 | ECC BUSHING 32-36-40-44 |
442.9642-01 | H4800 | ECC BSHG 24-28-32 |
442.9643-01 | H4800 | ECC BSG 13-16-20-24 |
442.7142-01 | H4800 | HUB |
442.7169-00 | H4800 | RING |
442.9609-01 | H4800 | KEY R 25X14X250 |
442.7093-00 | H4800 | GEAR & PINION SET SPIRAL BVL |
442.7171-01 | H4800 | ECC GEAR KEY |
442.7107-01 | H4800 | WEARING PLATE-ECC |
853.0646-00 | H4800 | PIN PRYM N 16 X 45 |
442.7163-01 | H4800 | HYDROSET CYLINDER |
442.7166-01 | H4800 | HYDROSET CYL BUSH |
873.0892-00 | H4800 | O-RING 530 X 7 SMS 1587 |
442.9672-00 | H4800 | HYD PISTON ASM H/ |
442.7122-01 | H4800 | PISTON WEARING PLT |
442.7121-01 | H4800 | STEP WASHER |
442.7112-00 | H4800 | CHEVRON PACKING-HYD |
442.7167-01 | H4800 | PACKING CLAMP PLATE |
442.9663-00 | H4800 | HYDROSET CYL COVER |
442.7202-01 | H4800 | HYD CYL COVER GASKT |
873.1276-00 | H4800 | O-RING |
442.9966-901 | H4800 | PINIONSHAFT ASSEMBLY |
442.7506-01 | H4800 | PINIONSHAFT HSG |
442.7136-01 | H4800 | PINSHAFT HSG GASKET |
442.7136-02 | H4800 | PINSHAFT HSG GASKET |
442.7136-03 | H4800 | PINSHAFT HSG GASKET |
868.0282-00 | H4800 | SPHER ROLLR BEARING |
868.0804-00 | H4800 | SPHER ROLLR BEARING |
442.7130-01 | H4800 | PINION END SPACER |
442.7131-01 | H4800 | SHEAVE END SPACER |
873.1208-00 | H4800 | OILSEAL RING BASL OILSEAL RI |
442.9684-01 | H4800 | PINSHAFT SEAL PLT PINION END |
442.7133-01 | H4800 | PINSHAFT SEAL PLATE |
442.7134-01 | H4800 | PINSHAFT SEALPLT GASKET |
442.7135-01 | H4800 | PINSHAFT SEALPLT GASKET |
442.7135-02 | H4800 | PINSHAFT SEALPLT GASKET |
853.0590-00 | H4800 | SPRING PIN PRYM N 8X28 |
442.9937-01 | H4800 | PINIONSHAFT |
857.0337-00 | H4800 | KEY T 22X14X95 SMS 2307 |
857.0336-00 | H4800 | KEY T 28X16X110 SMS 2307 |
900.0022-00 | H4800 | ELBOW 3/4 A4 127 1345, BLACK |
900.2026-00 | H4800 | MAGNETIC PLUG 3/4 |
873.0385-00 | H4800 | SEALING RING TREDO 20 |
442.7577-01 | H4800 | OIL LEVEL PLUG |
873.0108-00 | H4800 | O-RING 3.0X 34.2X 40.2 |
442.7578-01 | H4800 | PIPE-PINION END . |
442.8703-00 | H4800 | PINIONSHFT PUMP ASM 460V, 60HZ |
906.0367-00 | H4800 | PUMP P3-AAN-0, 75-FL-20-B0 1 |
906.0366-00 | H4800 | SPACER |
930.0248-00 | H4800 | COUPLING |
906.0365-00 | H4800 | FOOT FLANGE |
923.0193-00 | H4800 | PRESSURE GAUGE 2748 GLYC D 63 |
912.0129-00 | H4800 | FILTER CARTRIDGE PC 507 |
442.7238-01 | H4800 | WASHER-SHEAVE RETAINER |
442.7259-901 | H4800 | MAINSHAFT ASSM |
442.7100-01 | H4800 | MAINSHAFT |
442.7117-01 | H4800 | MAINSHAFT SLEEVE |
853.0119-00 | H4800 | PARALLEL PIN |
442.7120-01 | H4800 | MAINSHAFT STEP |
442.8332-01 | H4800 | HEAD CENTER |
442.7225-01 | H4800 | MANTLE A M1 |
442.7225-02 | H4800 | MANTLE A M2 |
442.7230-01 | H4800 | MANTLE B M1 |
442.7230-02 | H4800 | MANTLE B M2 |
442.8039-01 | H4800 | MANTLE EF M1 |
442.9073-03 | H4800 | MANTLE HC M7 |
442.7105-00 | H4800 | head nut with burning ring |
442.8333-01 | H4800 | HEADNUT-INNER S & |
442.7115-01 | H4800 | BURNING RING |
442.7102-01 | H4800 | DUST SEAL RING |
442.7103-01 | H4800 | RETAINER RING |
442.7523-01 | H4800 | DUST SEAL RETAINER |
442.7524-01 | H4800 | SCRAPER |
442.7180-00 | H4800 | TOPSHELL 2-ARM |
442.7190-01 | H4800 | SPIDER ARM SHIELD |
900.0425-00 | H4800 | PIPE COUPLING |
808.0220-00 | H4800 | STEEL PIPE 10 X 1,5 MM |
442.7492-01 | H4800 | SPIDER CAP |
912.0114-00 | H4800 | AIR FILTER PI0102 R1/4" + INS |
900.0169-00 | H4800 | NIPPLE 1/4 N8 131 6314, BLACK |
900.0002-00 | H4800 | ELBOW 1/4 A1 127 0016, BLACK |
873.0838-00 | H4800 | O-RING 5.7X499.3X510.7 |
442.9408-01 | H4800 | SPIDER BUSHING |
442.7193-01 | H4800 | OIL SEAL RING-SPIDR |
900.0981-00 | H4800 | PLUG KR1 INSEX ZN 10 |
442.8416-01 | H4800 | CONCAVE RNG EF M1 |
442.8417-01 | H4800 | CONCAVE RING F M1 |
442.8417-02 | H4800 | CONCAVE RING F M2 |
442.8417-03 | H4800 | CONCAVE RING F M7 |
442.8418-01 | H4800 | CONCAVE RNG MF M1 |
442.8418-02 | H4800 | CONCAVE RNG MF M2 |
442.8419-01 | H4800 | CONCAVE RING M M1 |
442.8419-02 | H4800 | CONCAVE RING M M2 |
442.8420-01 | H4800 | CONCAVE RNG MC M1 |
442.8420-02 | H4800 | CONCAVE RNG MC M2 |
442.8421-01 | H4800 | CONCAVE RING C M1 |
442.8421-02 | H4800 | CONCAVE RING C M2 |
442.8422-01 | H4800 | CONCAVE RNG EC M1 |
442.8422-02 | H4800 | CONCAVE RNG EC M2 |
442.7484-01 | H4800 | FILLER RING (F, MF) |
442.7485-01 | H4800 | FILLER RING EF,M,MC |
900.1821-00 | H4800 | PIPE 1-1/4 X 165 KREA SMS 1787 |
442.7251-02 | H4800 | WASHER-CONCAVE 80X30X140 |
442.7251-03 | H4800 | CONCAVE WASHER |
442.7252-01 | H4800 | SHIM 1X80X20 1142-32 |
442.7252-02 | H4800 | SHIM 3X80X20 -00 |
442.7252-03 | H4800 | SHIM 5X80X20 -00 |
442.7252-04 | H4800 | SHIM 10X80X20 -00 |
442.8687-01 | H4800 | SCREW M6S 30X360 8.8 |
442.7253-01 | H4800 | SLEEVE . |
442.7271-01 | H4800 | CONCAVE SUPT WASHER |
863.0058-00 | H4800 | DISC SPRING 90X46X5 |
442.8425-01 | H4800 | CONCAVE CLAMP RING |
442.8290-01 | H4800 | DOWEL PIN |
442.7267-90 | H4800 | FEED SPLITTER ASM LH |
442.7267-00 | H4800 | FEED SPLITTER ASM RH |
442.7191-00 | H4800 | FEED HOPPER ASM |
914.0170-00 | H4800 | OIL LEVEL INDICATOR 10" LG |
442.8345-01 | H4800 | HYDRAULIC PIPE |
902.0746-00 | H4800 | VALVE HRSF-3/4R 200KPA |
912.0127-00 | H4800 | PRESS DROP INDIC PIS3097/2,2 |
912.0116-00 | H4800 | AIR FILTER PI0121 |
923.0192-00 | H4800 | THERMOMETER IFC60 0-120 L100 |
930.0237-00 | H4800 | COUPLING HALF D38 05-32-540 |
906.0142-00 | H4800 | MECHANICAL SEAL 3884087 |
912.0126-00 | H4800 | FILTER CARTRIDGE PC230 |
442.2873-91 | H4800 | HEAT EXCHANGER BCF 602-0-4 |
910.0102-00 | H4800 | AIR-OIL COOLER-STD |
900.0160-00 | H4800 | BUSHING 2.00 X 1.50 |
906.0390-00 | H4800 | COMPLETE FAN-(6 BLADE FAN) |
910.0112-00 | H4800 | AXIAL FAN (4-BLADES) |
906.0309-00 | H4800 | IMPELLER BLADES-MK.002 |
906.0387-00 | H4800 | FAN BLADE |
910.0067-00 | H4800 | COOLER CORE IE-2927 |
972.0531-00 | H4800 | MOTOR, M2AA112M-4 3601 400VY |
912.0087-00 | H4800 | DIRT TRAP SW/0 1 1/2-0 |
902.0723-00 | H4800 | RELIEF VALVE DN32 0,7MPA 474122P H4 |
442.1774-00 | H4800 | FLOW SWITCH ASM |
930.0205-00 | H4800 | COUPLING HE 14 PUMPING UN |
930.0252-00 | H4800 | COUPLING ND 8 |
843.1445-00 | H4800 | STUD SCREW |
906.0270-00 | H4800 | PUMP P3BAN2004 HL10B02 |
906.0377-00 | H4800 | HYDROSET PUMP |
972.0182-00 | H4800 | MOTOR MT90L-2 2,2KW 220-380V |
906.0268-00 | H4800 | PUMP BRACKET BL 7SL PUMPING UNIT |
906.0376-00 | H4800 | PUMPBRACKET |
906.0269-00 | H4800 | FOOT BRACKET P200 PUMPING UNIT |
919.0165-00 | H4800 | ACCUMULATOR 25L OLAER |
919.0171-00 | H4800 | BLADDER COMPLETE 25L |
919.0184-00 | H4800 | BLADDER COMPLETE |
442.1954-01 | H4800 | ACCUMULATOR CLAMP |
442.8215-00 | H4800 | ACCUMULATOR CHARGING KIT |
900.0659-00 | H4800 | ADAPTER R2.0 X R2 |
442.6406-01 | H4800 | VALVE GUIDE BODY |
442.6402-01 | H4800 | CHK VALVE FLG FACE |
442.6403-01 | H4800 | VALVE |
442.6508-00 | H4800 | CONNECTION PIECE |
900.0655-00 | H4800 | ADAPTER R3/4 X R3/4 702-12-12 |
442.8179-00 | H4800 | ACCUM PIPE PROTECTOR (SET-L+R) |
912.0128-00 | H4800 | FILTER BASE |
923.0379-00 | H4800 | PRESSURE GAUGE M20-2 0-6MPA 6"DIA |
984.0530-00 | H4800 | IMMERSION HEATER OE3SB9/3-1650 440V |
984.0605-00 | H4800 | IMM HTR 440V,2190W |
912.0138-00 | H4800 | AIR FILTER PI0154 MIC |
912.0139-00 | H4800 | FILTER CARTRIDGE |
912.0113-00 | H4800 | AIR FILTER 504-2S 5 MICRON |
902.0645-00 | H4800 | AIR REGULATOR 216-2-8 |
923.0267-00 | H4800 | PRESSURE GAUGE |
864.0046-00 | H4800 | STAMP "B" RUBBER COMPRESSION MOUNT |
899.0099-00 | H4800 | LIFTING EYE BOLT |
442.0800-91 | H4800 | LEAD-CHECK OF C.S.S. |
442.7282-01 | H4800 | EYEBOLT-LIFTING PLATE |
442.7283-00 | H4800 | LIFTING TOOL-ECC SLV |
442.7281-00 | H4800 | LIFTING TOOL-BTMSHL BSG |
442.8043-00 | H4800 | LIFTING TOOL-BTMSHL BSG |
920.0110-00 | H4800 | SLUGGING WRENCH |
920.0151-00 | H4800 | SLUGGING WRENCH |
442.7284-00 | H4800 | LOWERING ROD W/NUTS |
843.1333-00 | H4800 | STUD BOLT |
442.7280-00 | H4800 | PISTON STOP PLATE |
442.8794-01 | S4800 | BTMSHELL SIDE LINER |
442.8796-01 | S4800 | BTMSHELL SIDE LINER |
442.8797-01 | S4800 | BTMSHELL SIDE LINER |
442.8798-01 | S4800 | BTMSHELL SIDE LINER |
442.8795-01 | S4800 | BTMSHELL SIDE LINER |
442.8068-01 | S4800 | ECCENTRIC |
442.8067-01 | S4800 | ECC BUSH 20-25-30-36 |
442.8092-901 | S4800 | MAINSHAFT SLV & DWL |
442.8063-01 | S4800 | HEADCENTER |
442.8070-01 | S4800 | MANTLE B M1 |
442.8070-02 | S4800 | MANTLE B M2 |
442.8089-01 | S4800 | MANTLE A M1 |
442.8089-02 | S4800 | MANTLE A M2 |
442.8059-01 | S4800 | TOPSHELL EC2 |
442.9036-01 | S4800 | TOPSHELL LINER |
442.8075-01 | S4800 | ARM SHEILD ASM |
442.8077-01 | S4800 | FIXING PIN |
442.8078-01 | S4800 | BUMPER |
442.8079-01 | S4800 | BUMPER |
442.8090-01 | S4800 | BRACKET-ADAPTER |
442.9164-00 | S4800 | SPIDER CAP |
442.8098-00 | S4800 | LWR CONCAVE C M1 |
442.8098-90 | S4800 | LWR CONCAVE C M2 |
442.8114-00 | S4800 | LWR CONCAVE EC M1 |
442.8114-90 | S4800 | LWR CONCAVE EC M2 |
452.0273-901 | S4800 | LWR CONCAVE MC M1 |
452.0273-902 | S4800 | LWR CONCAVE MC M2 |
442.8099-00 | S4800 | UPR CONCAVE C M1 |
442.8099-90 | S4800 | UPR CONCAVE C M2 |
442.8115-00 | S4800 | UPR CONCAVE EC M1 |
442.8115-90 | S4800 | UPR CONCAVE EC M2 |
452.0274-901 | S4800 | UPR CONCAVE MC M1 |
452.0274-902 | S4800 | UPR CONCAVE MC M2 |
442.8105-00 | S4800 | FEED HOPPER |
442.8645-00 | S4800 | HYDRAULIC HOSE GUARD |
442.1561-01 | S4800 | KEY-WOODEN WEDGE |
442.8735-00 | H6800 | BOTTOM SHELL ASM |
442.8760-00 | H6800 | PINIONSHAFT ARM LNR |
442.8759-00 | H6800 | NARROW ARM LINER |
900.2108-00 | H6800 | ELBOW 4" A4 SMS 435 |
442.8742-01 | H6800 | BOTTOM SHELL BUSH |
900.0921-00 | H6800 | TEE CPLG 3/4 SA 4072,415 |
900.1412-00 | H6800 | PIPE 3/4 X 70 KREA SMS 1787 |
442.8741-01 | H6800 | DUST COLLAR |
442.8762-01 | H6800 | LOCATING BAR |
442.8809-01 | H6800 | SHIM 0.1 THK(0.003) |
442.8809-02 | H6800 | SHIM 0.5 THK(0.02) |
442.8809-03 | H6800 | SHIM 0.7 THK(0.03) |
442.8809-04 | H6800 | SHIM 1.0 THK(0.04) |
442.8808-01 | H6800 | DUST COLLAR GASKT (2-PIECE) |
442.8747-01 | H6800 | INNER SEAL RING |
442.8733-01 | H6800 | ECCENTRIC |
442.8824-01 | H6800 | ECC BUSH 18+20+24+28 |
442.8825-01 | H6800 | ECC BUSH 28+32+36+40 |
442.8826-01 | H6800 | ECC BUSH 40+44+48+50 |
442.8743-00 | H6800 | RING (TWO PIECE) |
442.8723-00 | H6800 | GEAR & PINION SET (SOLD AS SET) |
442.8807-01 | H6800 | ECC GEAR KEY |
442.8761-01 | H6800 | WEARING PLATE-ECC |
442.8722-01 | H6800 | HYDROSET CYLINDER |
442.8724-01 | H6800 | HYDROSET CYL BUSH |
873.1152-00 | H6800 | O-RING 625 X7 SMS1587 |
442.8758-00 | H6800 | PISTON |
442.8730-01 | H6800 | PISTON WRG PLATE |
442.8731-01 | H6800 | STEP WASHER |
442.8739-00 | H6800 | CHEVRON PACKING |
442.8726-01 | H6800 | HYDROSET CYL COVER |
873.1153-00 | H6800 | O-RING 510 X5,7 SMS1587 |
442.8749-01 | H6800 | HYD CYL COVER GASKT HYD CYL CO |
442.8783-01 | H6800 | COVER PLATE CLOSURE PLUG |
984.0623-00 | H6800 | TRANSDUCER PROBE H/S |
442.8847-901 | H6800 | PINIONSHAFT ASSY (LESS PINION) |
442.8764-01 | H6800 | PINIONSHAFT HSG |
442.8803-01 | H6800 | PINSHAFT HSG GASKET |
442.8803-02 | H6800 | PINSHAFT HSG GASKET |
442.8803-03 | H6800 | PINSHAFT HSG GASKET |
868.0799-00 | H6800 | SPHERICAL ROLLER BEARING |
868.0806-00 | H6800 | SPHER ROLLER BEARNG |
442.8771-01 | H6800 | SPACER-SHV&PIN END |
873.1161-00 | H6800 | OIL SEAL RING CC OIL SEAL R |
442.8766-01 | H6800 | PINSHAFT SEAL PLT |
442.8765-01 | H6800 | PINSHAFT SEAL PLT |
442.8775-01 | H6800 | PINSHAFT SEALPLT GASKET |
442.8774-01 | H6800 | PINSHAFT SEALPLT GASKET |
442.8774-02 | H6800 | PINSHAFT SEALPLT GASKET |
442.8772-01 | H6800 | PINIONSHAFT |
857.0350-00 | H6800 | KEY T 25X14X95 SMS 2307 |
442.8778-01 | H6800 | OIL LEVEL PLUG |
442.8787-01 | H6800 | WASHER-SHEAVE RETAINER |
442.8788-01 | H6800 | SPACER-SHEAVE RETAINER |
442.8848-901 | H6800 | MAINSHAFT ASM |
442.8767-01 | H6800 | MAINSHAFT |
442.8792-01 | H6800 | MAINSHAFT SLEEVE |
853.0119-00 | H6800 | PARALLEL PIN |
442.8732-01 | H6800 | MAINSHAFT STEP |
442.8763-01 | H6800 | HEADCENTER |
442.8819-01 | H6800 | MANTLE A M1 |
442.8819-02 | H6800 | MANTLE A M2 |
442.8820-01 | H6800 | MANTLE B M1 |
442.8820-02 | H6800 | MANTLE B M2 |
442.8821-01 | H6800 | MANTLE D M1 |
442.8821-02 | H6800 | MANTLE D M2 |
442.9355-01 | H6800 | MANTLE EF M1 |
452.0820-001 | H6800 | MANTLE EEF M1 |
452.0820-002 | H6800 | MANTLE EEF M2 |
442.8800-00 | H6800 | HEADNUT W/BURN RING |
442.8791-01 | H6800 | INNER HEAD NUT **SEE I-NOTE* |
442.6427-01 | H6800 | BURNING RING |
442.8802-01 | H6800 | DUST SEAL RING |
442.8801-01 | H6800 | RETAINER RING |
442.8804-01 | H6800 | DUST SEAL RETAINER |
442.8805-01 | H6800 | SCRAPER |
442.8849-901 | H6800 | TOPSHELL EC2 |
442.8812-01 | H6800 | SPIDER ARM SHIELD |
900.0243-00 | H6800 | SCRENED SOCKET |
442.8753-01 | H6800 | SPIDER CAP |
873.1160-00 | H6800 | O-RING 529,3X5,7 SMS1587 |
442.8754-01 | H6800 | SPIDER BUSHING |
442.8755-01 | H6800 | OIL SEAL RING |
442.8813-01 | H6800 | CONCAVE RNG EC M1 |
442.8813-02 | H6800 | CONCAVE RNG EC M2 |
442.8814-01 | H6800 | CONCAVE RING C M1 |
442.8814-02 | H6800 | CONCAVE RING C M2 |
442.8815-01 | H6800 | CONCAVE RNG MC M1 |
442.8815-02 | H6800 | CONCAVE RNG MC M2 |
442.8816-01 | H6800 | CONCAVE RING M M1 |
442.8816-02 | H6800 | CONCAVE RING M M2 |
442.8817-01 | H6800 | CONCAVE RNG MF M1 |
442.8817-02 | H6800 | CONCAVE RNG MF M2 |
442.8818-01 | H6800 | CONCAVE RING F M1 |
442.8818-02 | H6800 | CONCAVE RING F M2 |
442.9356-01 | H6800 | CONCAVE RNG EF M1 |
442.9356-02 | H6800 | CONCAVE RNG EF M2 |
452.0832-001 | H6800 | CONCAVE EEF M1 |
452.0832-002 | H6800 | CONCAVE EEF M2 |
442.8823-01 | H6800 | FILLER RING (M & MC) |
442.8863-01 | H6800 | FILLER RING (F, MF) |
442.8881-01 | H6800 | WASHER-CONCAVE |
442.7252-01 | H6800 | SHIM 1X80X20 1142-32 |
442.7252-02 | H6800 | SHIM 3X80X20 -00 |
442.7252-03 | H6800 | SHIM 5X80X20 -00 |
442.7252-04 | H6800 | SHIM 10X80X20 -00 |
442.8908-01 | H6800 | HOSE |
442.9415-00 | H6800 | WEAR PLATE |
863.0058-00 | H6800 | DISC SPRING 90X46X5 |
442.8793-01 | H6800 | CONCAVE CLAMPING RING |
972.0532-00 | H6800 | MOTOR MBT112M 1800RPM 6HP LUBE |
843.1267-00 | H6800 | STUD SCREW 12X45 5,8 |
919.0170-00 | H6800 | BLADDER COMPLETE 20L |
919.0174-00 | H6800 | ACCUMULATOR ASM FOR BLADDE |
442.8777-00 | H6800 | CHECK VALVE |
900.2026-00 | H6800 | MAGNETIC PLUG 3/4 |
442.5904-01 | H6800 | FIXING PLATE & |
442.9781-00 | H6800 | TOP PLATE COMP MTG |
442.8879-00 | H6800 | LIFTING TOOL/ECC SL |
442.8880-00 | H6800 | LIFTING TOOL/BTM SHELL |
843.1511-00 | H6800 | STUD BOLT |
442.9042-01 | S6800 | ACCESS HOLE SIDE LNR |
442.9043-01 | S6800 | BSHELL SIDE LINER H/ |
442.9040-01 | S6800 | PINION ARM SIDE LINR |
442.9041-01 | S6800 | NARROW ARM SIDE LNR |
442.8973-01 | S6800 | ECCENTRIC |
442.9033-01 | S6800 | ECC BSHG 20-25-30-35-40 |
452.1700-901 | S6800 | MAINSHAFT ASY W/O MANTLE |
442.8971-01 | S6800 | MAINSHAFT |
442.8792-01 | S6800 | MAINSHAFT SLEEVE |
442.8974-01 | S6800 | HEADCENTER |
442.8982-01 | S6800 | MANTLE A M1 |
442.8982-02 | S6800 | MANTLE A M2 |
442.8983-01 | S6800 | MANTLE B M1 |
442.8805-01 | S6800 | SCRAPER |
442.8970-01 | S6800 | TOPSHELL |
442.8975-01 | S6800 | RIM LINER |
442.8976-01 | S6800 | SPIDER ARM SHIELD |
442.8969-00 | S6800 | SPIDER |
442.8977-01 | S6800 | SPIDER CAP |
442.8754-01 | S6800 | SPIDER BUSHING |
442.9071-90 | S6800 | LOWER CONCAVE RING C M2 |
442.8979-00 | S6800 | CONCAVE LWR EC M1 |
442.9071-00 | S6800 | CONCAVE LWR C M1 |
442.8981-00 | S6800 | CONCAVE UPR EC M1 |
442.9072-00 | S6800 | CONCAVE UPR C M1 |
442.9072-90 | S6800 | CONCAVE RING-UPR C M2 |
452.0317-901 | H8800 | PINIONSHAFT ARM LINERS |
452.0314-901 | H8800 | NARROW ARM LINER |
442.9396-00 | H8800 | BEND-ELBOW |
900.2199-00 | H8800 | FLANGE, PARTED SAE3000 4" |
873.0129-00 | H8800 | O-RING 3.0X109.4X115.5 |
442.9248-01 | H8800 | BOTTOMSHELL BUSHING |
442.9539-01 | H8800 | WEARING PLATE |
442.9539-02 | H8800 | WEARING PLATE |
442.9540-01 | H8800 | WEARING PLATE |
442.9541-01 | H8800 | WEARING PLATE |
442.9541-02 | H8800 | WEARING PLATE |
442.9542-01 | H8800 | WEARING PLATE |
442.9542-02 | H8800 | WEARING PLATE |
452.0313-901 | H8800 | BOTTOMSHELL LINERS |
442.9307-01 | H8800 | DUST COLLAR |
442.9309-01 | H8800 | RING |
442.9308-02 | H8800 | LOCATING BAR |
442.9362-01 | H8800 | SHIM 0,1 THK(0.003) |
442.9362-02 | H8800 | SHIM 0,5 THK(0.02) |
442.9362-03 | H8800 | SHIM 0,7 THK(0.03) |
442.9362-04 | H8800 | SHIM 1,0 THK(0.04) |
841.0256-00 | H8800 | CAPSCREW HEXSOC M10-1.50X 50 |
442.9363-01 | H8800 | DUST COLLAR GASKET |
442.9310-01 | H8800 | INNER SEAL RING |
847.0063-00 | H8800 | WASHER ZINC 10 X 26 X 65 |
442.9530-02 | H8800 | SCREW M6S 42X140 8.8 |
442.9245-01 | H8800 | ECCENTRIC |
442.9357-01 | H8800 | ECC BSHG 24/28/32/36 |
442.9358-01 | H8800 | ECC BSHG 36/40/44/48 |
442.9359-01 | H8800 | ECC BSHG 48/52/56/60 |
442.9360-01 | H8800 | ECC BSHG 60/64/68/70 |
442.9246-01 | H8800 | HUB |
442.9274-00 | H8800 | RING |
442.9469-01 | H8800 | KEY R 32X18X360 |
847.0181-00 | H8800 | SPRING WASHER M16 X 17X30 |
442.9311-00 | H8800 | GEAR & PINION SET SPIRAL BEV |
442.9275-01 | H8800 | ECCENTRIC GEAR KEY |
442.9249-02 | H8800 | ECC WEARING PLATE |
853.0646-00 | H8800 | PIN PRYM N 16 X 45 |
442.9253-01 | H8800 | HYDROSET CYLINDER |
442.9980-01 | H8800 | HYDROSET CYLINDER |
442.9256-01 | H8800 | HYDROSET CYL BUSH |
873.1211-00 | H8800 | O-RING SEE 873. |
442.9743-00 | H8800 | HYDROSET PISTON ASM |
853.0988-00 | H8800 | PARALLEL PIN |
442.9724-01 | H8800 | PISTON WEARING PLT |
442.9722-01 | H8800 | STEP WASHER |
442.9257-00 | H8800 | CHEVRON PACKING |
442.9304-01 | H8800 | PACKING CLAMP PLATE |
442.9255-00 | H8800 | HYDROSET CYL COVER |
873.1233-00 | H8800 | O-RING |
873.1210-00 | H8800 | O-RING |
442.9815-901 | H8800 | PINIONSHAFT ASSM |
442.9258-01 | H8800 | PINIONSHAFT HOUSING |
442.9806-01 | H8800 | PINION SHAFT HOUSING |
442.9364-01 | H8800 | PINSHAFT HSG GASKET 0,5 THK |
442.9364-02 | H8800 | PINSHAFT HSG GASKET 0,8 THK |
442.9364-03 | H8800 | PINSHAFT HSG GASKET 1,5 THK |
868.0832-00 | H8800 | SPHERICAL ROLLER BEARING |
00-813-252-007 | H8800 | SPHERICAL ROLLER BEARING |
868.0832-00 | H8800 | SPHERICAL ROLLER BEARING |
00-813-250-076 | H8800 | SPHERICAL ROLLER BEARING |
442.9334-01 | H8800 | PIN& SHV END SPACER |
442.9808-01 | H8800 | SPACER |
873.1219-00 | H8800 | SEAL RING |
442.9261-01 | H8800 | PINSHAFT SEAL PL PINION END |
442.9260-01 | H8800 | PINSHAFT SEAL PL SHEAVE END |
442.9365-01 | H8800 | PINSHAFT SEALPLT GASKET |
442.9366-01 | H8800 | PINSHAFT SEALPLT GASKET |
442.9366-02 | H8800 | PINSHAFT SEALPLT GASKET |
853.0590-00 | H8800 | SPRING PIN PRYM N 8X28 |
442.9259-01 | H8800 | PINIONSHAFT |
442.9807-01 | H8800 | PINION SHAFT |
857.0353-00 | H8800 | KEY |
857.0354-00 | H8800 | KEY |
842.0020-00 | H8800 | SCREW |
442.9346-01 | H8800 | OIL LEVEL PLUG |
442.9342-01 | H8800 | WASHER-SHEAVE RETAINER |
442.9343-01 | H8800 | SPACER |
442.9732-AD | H8800 | MAINSHAFT ASM |
452.9998-901 | H8800 | MAINSHAFT ASSEMBLY |
442.9294-01 | H8800 | MAINSHAFT SLEEVE |
853.0988-00 | H8800 | PARALLEL PIN |
442.9723-01 | H8800 | MAINSHAFT STEP |
442.9314-01 | H8800 | MANTLE A M1 |
442.9339-01 | H8800 | MANTLE B M1 |
442.9340-01 | H8800 | MANTLE EF M1 **I-NOTE** |
442.9270-00 | H8800 | HEADNUT W/BURN RING |
442.9269-01 | H8800 | INNER HEADNUT |
442.9306-01 | H8800 | BURNING RING |
442.9271-01 | H8800 | DUST SEAL RING |
442.9272-01 | H8800 | RETAINING RING |
442.9367-01 | H8800 | SCRAPER RETAINER |
442.9368-01 | H8800 | SCRAPER |
442.9265-00 | H8800 | SPIDER ARM SHIELD *I-NOTE* |
452.0266-001 | H8800 | SPIDER CAP |
873.1232-00 | H8800 | O-RING- 790,0 X 5,7 SMS 1586 |
442.9266-01 | H8800 | SPIDER BUSH ALL THS |
191.2376-00 | H8800 | TEMPERATURE TRANSMITTER |
452.0418-001 | H8800 | OIL SEAL RING/SCRAPER |
452.0417-001 | H8800 | RING |
452.0419-001 | H8800 | SUPPORT RING |
442.9312-01 | H8800 | CONCAVE RNG MF M1 |
442.9336-01 | H8800 | CONCAVE RING EC M1 |
442.9337-01 | H8800 | CONCAVE RING M M1 |
442.9398-01 | H8800 | CONCAVE RING C M1 |
442.9471-01 | H8800 | CONCAVE RNG MC M1 |
442.9520-00 | H8800 | FILLER RING MC |
442.9352-01 | H8800 | WASHER |
452.1068-001 | H8800 | WASHER |
840.1136-00 | H8800 | SCREW |
442.9353-01 | H8800 | SLEEVE |
442.9354-01 | H8800 | WASHER |
863.0015-00 | H8800 | DISC SPRING |
442.9313-01 | H8800 | SUPPORT RING |
442.9521-00 | H8800 | SPLITTER RH |
442.9521-90 | H8800 | SPLITTER LH |
906.0412-00 | H8800 | MECHANICAL SEAL 3884087 |
910.0104-00 | H8800 | AIR-OIL COOLER-STD |
442.9485-08 | H8800 | ROD SQ 12 L=80 |
442.9485-09 | H8800 | ROUND BAR L=100 |
442.9490-01 | H8800 | HYDRAULIC HOSE R1" X 2100 |
442.9491-01 | H8800 | HYDRAULIC HOSE R3/4" X 2700 |
65-735-791-001 | H8800 | CONVERSION ADAPTER 0.50BSPP MALE - 0 |
65-735-791-002 | H8800 | CONVERSION ADAPTER 1.00BSPP MALE - 1 |
902.0061-00 | H8800 | VALVE 1/4" FT 110 |
902.0761-00 | H8800 | SHUT-OFF VALVE 7640-3/8" |
452.0264 | H8800 | Concave |
10-314-628-000 | 806JM | LOWER SIDE LINER |
10-314-627-000 | 806JM | UPPER SIDE LINER |
10-314-630-000 | 806JM | SUPPORT BAR 2306-0 |
400.0465-001 | 806JM | STAT JAW PL CORRUG M1 |
400.0465-002 | 806JM | STAT JAW PL CORRUG M2 |
10-314-625-000 | 806JM | WEDGE 2310-0 |
53-468-022-000 | 806JM | PROTECTION PLATE 2300-0 |
53-267-931-000 | 806JM | SHAFT ECCENTRIC |
00-813-249-006 | 806JM | SPHERICAL ROLLER BEARING CYLINDRICAL |
10-314-513-000 | 806JM | SW JAW COUNTER FLANGE SWING JAW |
10-314-512-000 | 806JM | SWING JAW SEAL PLATE |
10-314-514-000 | 806JM | COUNTER FLANGE INNER BRG |
10-314-515-000 | 806JM | FRAME OUTER COVER |
00-923-203-225 | 806JM | SEAL V-RING D255 X 25 |
00-813-249-005 | 806JM | SPHERICAL ROLLER BEARING TAPERED |
00-819-163-244 | 806JM | ADAPTER SLEEVE AH2344H |
10-314-516-000 | 806JM | FRAME OUTER LABYRINTH |
59-425-417-009 | 806JM | KEY 25 X 45 X 120 |
53-467-374-000 | 806JM | SPACER RING |
400.0464-001 | 806JM | SWING JAW PL CORRUG M1 |
400.0464-002 | 806JM | SWING JAW PL CORRUG M2 |
10-314-626-000 | 806JM | DEFLECTOR PLATE |
10-314-624-000 | 806JM | TOGGLE SEAT BLOCK |
10-314-632-000 | 806JM | TOGGLE SEAT |
10-314-634-000 | 806JM | TOGGLE PLATE |
53-467-395-500 | 806JM | TENSION ROD CLEVIS |
53-466-415-004 | 806JM | THREADED ROD |
127.0006-12 | 806JM | SPRING, TENSION ROD |
53-367-366-500 | 806JM | TENSION ROD WASHER |
53-267-383-500 | 806JM | LEFT BEARING HOUSING |
10-214-509-500 | 806JM | RIGHT BEARING HOUSING |
400.0474 | 806JM | WT Jaw plate |
10-314-404-000 | 907JM | LOWER SIDE LINER , 1206 |
10-314-386-000 | 908JM | UPPER SIDE LINER-CAST , 1206 |
10-314-481-000 | 909JM | WEDGE PLATE |
400.0314-002 | 910JM | BOLT M20X160 |
845.0010-00 | 911JM | HEX NUT-ZINC M20-2.50 |
847.0132-00 | 912JM | WASHER ZINC M20 3X21X36 |
400.0418-002 | 913JM | STAT JAW PL CG M2 |
10-314-429-000 | 914JM | WEDGE SWING JAW |
00-920-144-909 | 915JM | WEDGE BOLT ZINC |
53-467-117-000 | 916JM | PROTECTION PLATE |
53-267-115-000 | 917JM | SHAFT-ECCENTRIC |
00-813-249-006 | 918JM | SPHERICAL ROLLER BEARING CYLINDRICAL |
10-314-513-000 | 919JM | SW JAW COUNTER FLANGE SWING JAW |
10-314-512-000 | 920JM | SWING JAW SEAL PLATE |
10-314-514-000 | 921JM | COUNTER FLANGE INNER BRG |
10-314-515-000 | 922JM | FRAME OUTER COVER |
00-923-203-225 | 923JM | SEAL V-RING D255 X 25 |
00-813-249-005 | 924JM | SPHERICAL ROLLER BEARING TAPERED |
00-819-163-244 | 925JM | ADAPTER SLEEVE AH2344H |
10-314-516-000 | 926JM | FRAME OUTER LABYRINTH |
59-425-417-009 | 927JM | KEY 25 X 45 X 120 |
53-467-374-000 | 928JM | SPACER RING |
53-467-117-000 | 929JM | PROTECTION PLATE |
10-314-481-000 | 930JM | WEDGE PLATE |
400.0417-002 | 931JM | SWING JAW PLATE CRG M2 |
10-314-429-000 | 932JM | WEDGE SWING JAW |
10-314-479-000 | 933JM | DEFLECTOR PLATE |
10-314-517-000 | 934JM | TOGGLE SEAT BLOCK |
89-242-876-000 | 935JM | TOGGLE SEAT |
89-242-877-000 | 936JM | TOGGLE PLATE |
53-368-317-501 | 937JM | HYDRAULIC JACK ASM 5 TON |
53-467-395-500 | 938JM | TENSION ROD CLEVIS |
53-466-415-004 | 939JM | THREADED ROD |
127.0006-12 | 940JM | SPRING, TENSION ROD |
53-367-366-500 | 941JM | TENSION ROD WASHER |
53-267-383-500 | 942JM | LEFT BEARING HOUSING |
10-214-509-500 | 943JM | RIGHT BEARING HOUSING |
400.0483 | 943JM | WT Jaw plate |
10-314-263-000 | 1108JM | SIDE LINER-LWR (CAST) /1208 |
10-314-262-000 | 1108JM | SIDE LINER-UPPER (CAST) /1208 |
10-214-269-000 | 1108JM | WEDGE PLATE , 1208 |
400.0314-003 | 1108JM | SQUARE BOLT M20X180 |
845.0010-00 | 1108JM | HEX NUT-ZINC M20-2.50 |
65-651-001-015 | 1108JM | WASHER 3 X 21X 37 |
400.0410-002 | 1108JM | STATIONARY JAW PL CORRUG M2 |
400.0436-001 | 1108JM | STAT/SWING JAW PLATE WT(Z) M1 |
400.0437-001 | 1108JM | STAT JAW PL COARSE CORRUG M1 |
10-314-385-000 | 1108JM | WEDGE - SWING JAW |
00-920-144-909 | 1108JM | WEDGE BOLT ZINC |
53-267-444-000 | 1108JM | ECCENTRIC SHAFT |
00-813-249-004 | 1108JM | SPHER. BRG 24606CC/W33/C3 |
10-214-414-000 | 1108JM | SW JAW COUNTR FLANGE |
10-214-388-000 | 1108JM | SWING JAW FLANGE/1206 |
10-214-415-000 | 1108JM | COUNTERFLANGE INNER |
10-214-416-000 | 1108JM | FRAME OUTER COVER |
873.1327-00 | 1108JM | SEAL V-RING |
873.0910-00 | 1108JM | SEAL V-RING |
00-813-249-003 | 1108JM | SPHER BRG 23152 CK/W33/C3 |
00-819-163-352 | 1108JM | ADAPTER SLEEVE AH3152 . |
10-214-417-000 | 1108JM | FRAME OUTR LABERYNTH |
00-819-137-244 | 1108JM | LOCKWASHER-BEARING MB - 44 |
00-819-121-044 | 1108JM | LOCKNUT-BEARING NO-HM44T |
53-467-327-000 | 1108JM | SPACER RING |
00-930-920-033 | 1108JM | BEARING LOCKNUT KM32 |
53-466-783-000 | 1108JM | PROTECTION PLATE |
10-214-269-000 | 1108JM | WEDGE PLATE /1208 |
400.0409-002 | 1108JM | SWING JAW PLATE CORRUG M2 |
400.0433-001 | 1108JM | SWING JAW PL COARSE CORRUG M1 |
10-314-385-000 | 1108JM | WEDGE - SWING JAW |
59-942-843-001 | 1108JM | SCREW M33 x 880 |
10-214-384-000 | 1108JM | DEFLECTOR PLATE |
10-314-522-000 | 1108JM | TOGGLE SEAT BLOCK |
89-242-895-000 | 1108JM | TOGGLE SEAT |
89-242-894-000 | 1108JM | TOGGLE PLATE |
53-368-317-501 | 1108JM | HYDRAULIC JACK ASM 5 TON |
53-366-774-500 | 1108JM | HYDRAULIC CYL ROD |
53-466-668-500 | 1108JM | TENSION ROD CLEVIS 1208 |
53-466-415-001 | 1108JM | THREADED ROD 1208 |
17-202-779-001 | 1108JM | SPRING, TENSION ROD 1208/ |
53-166-775-500 | 1108JM | LEFT BEARING HSG/1206 |
10-114-387-500 | 1108JM | RIGHT BRG HSG /1206 |
53-473-796-003 | 1108JM | BOLT |
10-314-404-000 | 1206JM | LOWER SIDE LINER 1206 |
10-314-386-000 | 1206JM | UPPER SIDE LINER-CAST 1206 |
10-214-269-000 | 1206JM | WEDGE PLATE /1208 |
400.0314-003 | 1206JM | SQUARE BOLT M20X180 |
400.0415-002 | 1206JM | STATIONARY JAW PL CORRUG M2 1206 |
10-314-246-000 | 1206JM | WEDGE STA JAW 1206/1208 |
00-920-144-909 | 1206JM | WEDGE BOLT ZINC |
53-266-909-000 | 1206JM | ECCENTRIC SHAFT 1206 |
00-813-249-004 | 1206JM | SPHER. BRG 24606CC/W33/C3 SPHERICAL |
873.1327-00 | 1206JM | SEAL V-RING |
873.0910-00 | 1206JM | SEAL V-RING |
00-813-249-003 | 1206JM | SPHER BRG 23152 CK/W33/C3 SPHERICAL |
00-819-163-352 | 1206JM | ADAPTER SLEEVE AH3152 . |
10-214-417-000 | 1206JM | FRAME OUTR LABERYNTH |
00-819-137-244 | 1206JM | LOCKWASHER-BEARING MB - 44 |
00-819-121-044 | 1206JM | LOCKNUT-BEARING NO-HM44T |
53-466-918-000 | 1206JM | PROTECTION PLATE 1206 |
400.0414-002 | 1206JM | SWING JAW PLATE CORRUG M2 1206 |
10-314-246-000 | 1206JM | WEDGE STA JAW 1206/1208 |
10-214-255-000 | 1206JM | DEFLECTOR PLATE 1206/1208 |
10-314-425-000 | 1206JM | TOGGLE SEAT BLOCK 1206 |
89-242-707-000 | 1206JM | TOGGLE SEAT 1206 |
10-214-523-000 | 1206JM | TOGGLE PLATE 1208 |
53-467-347-000 | 1206JM | SHIM /1206 |
53-368-317-501 | 1206JM | HYDRAULIC JACK ASM 5 TON |
53-466-668-500 | 1206JM | TENSION ROD CLEVIS 1208 |
53-466-415-003 | 1206JM | THREADED ROD 1206 |
17-202-779-001 | 1206JM | SPRING, TENSION ROD 1208/ |
400.0450-001 | 1206JM | SPRING TENSION ROD |
53-166-775-500 | 1206JM | LEFT BEARING HSG/1206 |
10-114-387-500 | 1206JM | RIGHT BRG HSG /1206 |
10-314-263-000 | 1208JM | SIDE LINER-LWR (CAST)1208 SIDE LINER |
10-314-262-000 | 1208JM | SIDE LINER-UPPER (CAST) 1208 |
10-214-269-000 | 1208JM | WEDGE PLATE 1208 |
400.0314-002 | 1208JM | BOLT M20X160 |
400.0408-002 | 1208JM | STATIONARY JAW PL CORRUG M2 1208 |
400.0411-001 | 1208JM | STAT/SWING JAW PLATE WT(Z) M1 1208 |
400.0413-002 | 1208JM | STATIONARY JAW PLATE HD M2 1208 |
400.0425-001 | 1208JM | STAT JAW PL CORRUG COARSE M1 1208 |
10-314-246-000 | 1208JM | WEDGE STA JAW 1206/1208 |
53-466-463-000 | 1208JM | PROTECTION PLATE 1208 |
53-266-357-000 | 1208JM | ECCENTRIC SHAFT 1208 |
53-267-179-000 | 1208JM | ECCENTRIC SHAFT 1208/ |
00-813-249-002 | 1208JM | SPHERICAL ROLLER BEARING CYLINDRICAL |
402.7388-01 | 1208JM | SPACING COLLAR-LABYR /1208 |
402.7389-00 | 1208JM | LABYRINTH COVER & PLUGS |
32-402-739-101 | 1208JM | SPACER,INR LABYRINTH 1208 |
32-402-739-001 | 1208JM | SEALPLATE,INNER LABY 1208 |
00-923-203-315 | 1208JM | SEAL V RING |
00-813-249-001 | 1208JM | SPHERICAL ROLLER BEARING |
00-819-163-364 | 1208JM | ADAPTER SLEEVE AH3164H *i-note* |
402.7392-01 | 1208JM | LABYRINTH RING-OUTER |
00-819-137-256 | 1208JM | LOCKWASHER-BEARING MB- 56 |
00-930-920-056 | 1208JM | BEARING LOCKNUT TR280X4 1208// |
00-920-241-105 | 1208JM | SCREW M20X200 |
10-114-743-000 | 1208JM | SWING JAW PL 1208 **I-NOTE** |
400.0407-002 | 1208JM | SWING JAW PLATE CORRUG M2 1208 |
400.0420-001 | 1208JM | SWING JAW PL COARSE CORRUG M1 1208 |
10-214-255-000 | 1208JM | DEFLECTOR PLATE 1206/1208 |
53-467-202-000 | 1208JM | SAFETY KEY |
10-314-265-000 | 1208JM | TOGGLE SEAT BLOCK 1208 |
10-314-495-000 | 1208JM | TOGGLE SEAT BLOCK 1208 |
17-201-650-001 | 1208JM | TOGGLE SEAT |
10-214-523-000 | 1208JM | TOGGLE PLATE 1208 |
53-466-668-500 | 1208JM | TENSION ROD CLEVIS 1208 |
53-466-415-001 | 1208JM | THREADED ROD 1208 |
17-202-779-001 | 1208JM | SPRING, TENSION ROD 1208/ |
53-366-376-500 | 1208JM | WASHER,TENSION ROD 1208 |
53-366-379-500 | 1208JM | PUSHER PLATE- /1206/1208 |
10-114-256-502 | 1208JM | BEARING HSG MACH LH 1208 |
10-114-256-501 | 1208JM | BEARING HSG MACH RH 1208 |
53-466-431-001 | 1208JM | STUD |
402.4239-01 | 1211JM | SIDE LINER, UPPER |
402.4635-01 | 1211JM | CHEEK PLATE LOWER |
402.4258-00 | 1211JM | JAW PLATE SUPT STRIP |
400.0444-001 | 1211JM | STAT JAW PL COARSE CORRUG M1 |
400.0444-002 | 1211JM | STAT JAW PL COARSE CORRUG M2 |
400.0426-001 | 1211JM | STAT JAW PLATE HD M1 |
400.0427-001 | 1211JM | STAT JAW PLT MIDDLE |
402.4570-00 | 1211JM | TENSIONING STRIP |
53-267-179-000 | 1211JM | ECCENTRIC SHAFT 1208/ |
00-813-250-086 | 1211JM | SPHERICAL ROLLER BEARING |
873.1025-00 | 1211JM | V-RING |
00-813-249-001 | 1211JM | SPHERICAL ROLLER BEARING |
00-819-163-364 | 1211JM | ADAPTER SLEEVE AH3164H |
400.0443-001 | 1211JM | SWING JAW PL COARSE CORRUG M1 |
400.0443-002 | 1211JM | SWING JAW PL COARSE CORRUG M2 |
400.0423-001 | 1211JM | SWING JAW PLATE- HD |
402.2043-01 | 1211JM | SW JAW PLATE-MIDDLE |
402.2320-00 | 1211JM | TENSIONING STRIP |
402.4270-01 | 1211JM | TOGGLE SEAT HOLDER |
402.4607-01 | 1211JM | TOGGLE PLATE |
402.4303-00 | 1211JM | RETRACTION BAR L1340 |
402.4303-91 | 1211JM | RETRACTION BAR L=1500 |
127.0006-27 | 1211JM | SPRING,TENSION ROD |
400.044 | 1211JM | |
400.0442 | 1211JM | |
400.0438 | 1211JM | |
400.4039 | 1211JM | |
400.0422 | 1211JM | |
400.0421 | 1211JM | |
10-214-352-000 | 1312JM | LOWER SIDE LINER |
10-214-351-000 | 1312JM | UPPER SIDE LINER |
10-314-356-000 | 1312JM | WEDGE PLATE |
400.0445-001 | 1312JM | STAT/SWING JAW PL WT(Z) M1 |
400.0447-001 | 1312JM | STAT JAW PL CORRUGATED M1 |
400.0963-001 | 1312JM | STAT JAW PL SHARP TOOTHED M1 |
10-214-355-000 | 1312JM | WEDGE-SWING JAW |
53-366-632-501 | 1312JM | SCREW TAPERED HEAD |
53-466-616-000 | 1312JM | PROTECTION PLATE |
53-267-239-000 | 1312JM | ECCENTRIC SHAFT |
00-813-249-008 | 1312JM | SPHERICAL ROLLER BEARING CYLINDRICAL |
32-402-330-200 | 1312JM | SPACER, SWING JAW |
32-402-330-100 | 1312JM | SEALPLATE, SWING JAW |
32-402-396-700 | 1312JM | SPACER, INR LABYRINTH |
32-402-419-900 | 1312JM | SEALPLATE, INNER *I-Note* |
00-923-203-405 | 1312JM | SEAL V-RING D405 X 25 |
00-813-249-007 | 1312JM | SPHERICAL ROLLER BEARING TAPERED |
00-819-163-376 | 1312JM | ADAPTER SLEEVE AH3176H |
32-402-396-900 | 1312JM | SPACER,OUTR LABYRINTH |
00-819-121-168 | 1312JM | LOCKNUT-BEARING HM3168 |
400.0446-001 | 1312JM | SWING JAW PLT CORRUGATED M1 |
400.0964-001 | 1312JM | SWING PL SHARP TOOTHED M1 |
10-114-354-000 | 1312JM | DEFLECTOR PLATE |
53-466-927-000 | 1312JM | WEDGE HEAD BOLT |
10-314-500-000 | 1312JM | TOGGLE SEAT BLOCK |
17-201-650-001 | 1312JM | TOGGLE SEAT |
10-214-535-000 | 1312JM | TOGGLE PLATE 775 |
53-466-629-500 | 1312JM | TENSION ROD CLEVIS |
53-466-415-002 | 1312JM | THREADED ROD |
400.0450-001 | 1312JM | SPRING TENSION ROD |
53-366-624-500 | 1312JM | MOVABLE SPRING PLATE |
10-114-459-500 | 1312JM | LEFT BEARING HSG |
53-167-007-500 | 1312JM | RIGHT BEARING HSG |
53-466-623-000 | 1312JM | GUIDE BOLT BRG HSG |
402.4521-01 | 1511JM | CHEEK PLATE, UPPER |
402.4522-01 | 1511JM | CHEEK PLATE, LOWER |
402.4386-00 | 1511JM | SUPPORT STRIP |
402.4386-00 | 1511JM | SUPPORT STRIP |
400.0485-001 | 1511JM | STAT JAW PLATE COARSE CORRUG M1 |
400.0409-001 | 1511JM | STAT JAW PL SHARP TOOTHED M1 |
402.4501-01 | 1511JM | STAT/SWING JAW PLATE HD M1 1511 |
402.4502-01 | 1511JM | STAT/SWING JAW PLT MID HD M1 1511 |
650.0313-01 | 1511JM | SCREW M48 X 420 |
402.4330-02 | 1511JM | ECCENTRIC SHAFT |
00-813-250-093 | 1511JM | SPHERICAL ROLLER BEARING |
873.0907-00 | 1511JM | V-RING |
00-813-249-009 | 1511JM | SPHERICAL ROLLER BRG P/N 24176C |
402.4501-01 | 1511JM | STAT/SWING JAW PLATE HD M1 1511 |
400.0488-001 | 1511JM | SWING JAW PL COARSE CORRUG M1 |
400.0491-001 | 1511JM | SWING JAW PL SHARP TOOTHED M1 |
402.4502-01 | 1511JM | STAT/SWING JAW PLT MID HD M1 1511 |
402.2005-01 | 1511JM | TENSION STRIP, MOVABLE |
402.4508-01 | 1511JM | TOGGLE SEAT HOLDER |
402.4507-01 | 1511JM | TOGGLE SEAT |
402.4352-01 | 1511JM | TOGGLE SEAT |
402.4605-00 | 1511JM | TOGGLE PLATE L=950 1511 & 151 |
402.4469-91 | 1511JM | RETRACTION BAR 1511 |
127.0026-01 | 1511JM | SPRING 545 F/LENGTH |
402.4362-01 | 1513JM | CHEEK PLATE LOWER |
402.4361-01 | 1513JM | CHEEK PLATE-UPPER |
402.4386-00 | 1513JM | SUPPORT STRIP |
402.6036-01 | 1513JM | STAT JAW PL HD |
402.4396-01 | 1513JM | STAT JAW PLATE-MID |
402.5793-01 | 1513JM | TENSIONING STRIP, FIX TENSIONING |
650.0313-01 | 1513JM | SCREW M48 X 420 |
402.4330-01 | 1513JM | ECCENTRIC SHAFT |
00-813-250-093 | 1513JM | SPHERICAL ROLLER BEARING |
873.0907-00 | 1513JM | V-RING |
00-813-249-009 | 1513JM | SPHERICAL ROLLER BRG P/N 24176C |
400.0460-001 | 1513JM | SWING JAW PLATE HD M1 |
400.0461-001 | 1513JM | SW JAW PL MID WEDGE HD M1 |
402.2005-01 | 1513JM | TENSION STRIP, MOVABLE |
402.4345-01 | 1513JM | TOGGLE SEAT HOLDER |
402.4352-01 | 1513JM | TOGGLE SEAT |
402.4381-00 | 1513JM | TOGGLE PLATE |
402.4303-00 | 1513JM | RETRACTION BAR L1340 |
127.0006-27 | 1513JM | SPRING,TENSION ROD |
485.0001-001 | VSI | FEED TUBE FABRICATED |
485.0003-001 | VSI | FEED EYE RING SINGLE POSITION |
485.0004-901 | VSI | TIP SET 500 SILVER TILE |
485.0006-901 | VSI | TIP SET 500 WHITE TILE |
485.0008-901 | VSI | TIP CARRIER WEAR PLATE SET RED |
485.0010-901 | VSI | TRAIL PLATE SET |
485.0012-901 | VSI | CAVITY WEAR PLATE SET W/BOLTS |
485.0014-901 | VSI | ROTOR, 500 OPEN SIDED BARE |
485.0020-001 | VSI | ROTOR TAPER LOCK |
485.0023-901 | VSI | ROTOR WELDMENT, 500 OPEN SIDED |
485.0024-001 | VSI | DISTRIBUTOR PLATE HI-CHROME |
485.0025-901 | VSI | UPPER WEAR PLATE SET HI-CHROME |
485.0027-901 | VSI | LOWER WEAR PLATE SET HI-CHROME |
485.0029-901 | VSI | TOP WEAR PLATE SET - FULL DIAMETER |
485.0031-901 | VSI | TUNGSTEN EDGED TRAIL PLATE SET |
485.0033-901 | VSI | TRAIL PLATE SET |
485.0035-901 | VSI | ROTOR, 690 BARE O-S UNIVERSAL |
485.0045-001 | VSI | TOP PLATE FOR 27" ROTOR |
485.0046-001 | VSI | ROTOR TAPER LOCK |
485.0048-901 | VSI | ROTOR WELDMENT, 690 O-S UNIVERSAL |
485.0049-901 | VSI | UPPER WEAR PLATE SET HI-CHROME |
485.0051-901 | VSI | LOWER WEAR PLATE SET HI-CHROME |
485.0053-901 | VSI | TOP WEAR PLATE SET FULL DIAMETER |
485.0055-001 | VSI | FEED TUBE |
485.0056-001 | VSI | FEED EYE RING SINGLE POSITION |
485.0057-901 | VSI | TIP SET GREEN X-HARD PLATE |
485.0060-901 | VSI | TIP SET 690 BLUE HARD PLATE |
485.0061-901 | VSI | TIP CARRIER WEAR PLATE SET RED |
485.0063-901 | VSI | TRAIL PLATE SET NARROW |
485.0065-901 | VSI | TRAIL PLATE SET WIDE |
485.0067-901 | VSI | TRAIL PLATE SET STRAIGHT |
485.0069-901 | VSI | BACK UP TIP SET |
485.0072-901 | VSI | CAVITY WEAR PLATE SET W/BOLTS |
485.0073-901 | VSI | ROTOR 690 OPEN SIDED BARE |
485.0083-001 | VSI | DISTRIBUTOR PLATE FLAT HI-CHROME |
485.0083-901 | VSI | ROTOR WELDMENT - 690 OPEN SIDED |
485.0084-001 | VSI | DISTRIBUTOR PLATE CONE HI-CHROME |
485.0085-901 | VSI | UPPER WEAR PLATE SET HI-CHROME |
485.0087-901 | VSI | LOWER WEAR PLATE SET HI-CHROME |
485.0089-901 | VSI | TOP WEAR PLATE SET - FULL DIAMETER |
485.0091-001 | VSI | FEED TUBE |
485.0092-901 | VSI | ROTOR - 760 OPEN SIDED BARE |
485.0099-901 | VSI | ROTOR WELDMENT - 760 OPEN SIDED |
485.0100-901 | VSI | FEED EYE RING, BOLT ON HI-CHROME |
485.0101-901 | VSI | UPPER WAER PLATE SET 760 HI-CHROME |
485.0103-901 | VSI | LOWER WEAR PLATE SET 760 HI-CHROME |
485.0105-901 | VSI | TOP WEAR PLATE SET |
485.0107-901 | VSI | TRAIL PLATE SET - WIDE |
485.0109-901 | VSI | TRAIL PLATE SET - NARROW |
485.0111-901 | VSI | ROTOR-DEEP 840 O-S BARE MKII |
485.0118-001 | VSI | ROTOR BOSS MK II |
485.0119-001 | VSI | TAPERLOCK |
485.0120-001 | VSI | TOP PLATE |
485.0121 | VSI | UPPER WEAR PLATE KEEPER |
485.0122 | VSI | LOWER WEAR PLATE KEEPER |
485.0124 | VSI | WEAR PLATE CLIP |
485.0125-901 | VSI | ROTOR-DEEP 840 O-S BARE MKIII |
485.0126-901 | VSI | ROTOR WELDMENT DEEP 840 O-S |
485.0127-901 | VSI | TRAIL PLATE SET - WIDE |
485.0129-901 | VSI | ROTOR-DEEP 990 O-S MKIII |
485.0138-901 | VSI | ROTOR WELDMENT DEEP 990 O-S |
485.0139-001 | VSI | FEED TUBE |
485.0140-001 | VSI | FEED EYE RING SINGLE POSITION |
485.0141-901 | VSI | UPPER WEAR PLATE SET HI-CHROME |
485.0143-901 | VSI | LOWER WEAR PLATE SET 840 HI-CHROME |
485.0145-901 | VSI | ROTOR 840 O-S BARE MKII |
485.0152-901 | VSI | ROTOR 840 O-S BAR MKIII |
485.0153-901 | VSI | ROTOR WELDMENT 840 OPEN SIDED |
485.0154-901 | VSI | TOP WEAR PLATE SET |
485.0156-001 | VSI | DISTRIBUTOR PLATE BOLT |
485.0157-001 | VSI | FEED EYE RING SINGLE POSITION |
485.0158-901 | VSI | UPPER WEAR PLATE SET HI-CHROME |
485.0160-901 | VSI | LOWER WEAR PLATE SET HI-CHROME |
485.0162-901 | VSI | TIP SET ONE PIECE X/HARD PLATE |
485.0164-901 | VSI | TIP SET ONE PIECE BLUE HARD PLATE |
485.0165-901 | VSI | TIP SET SPLIT GREEN X-HARD PLATE |
485.0167-901 | VSI | TIP SET SPLIT BLUE HARD PLATE |
485.0168-901 | VSI | TRAIL PLATE SET NARROW |
485.0170-901 | VSI | TRAIL PLATE SET WIDE |
485.0172-901 | VSI | TRAIL PLATE SET STRAIGHT |
485.0174-901 | VSI | BACK UP TIP SET |
485.0184-901 | VSI | ROTOR 990 O-S BARE MKIII |
485.0185-901 | VSI | ROTOR WELDMENT 990 O-S |
485.0186-001 | VSI | DISTRIBUTOR PLATE FLAT HI-CHROME |
485.0187-001 | VSI | DISTRIBUTOR PLATE HEAVY HI-CHROME |
485.0188-901 | VSI | T/CWP SET SINGLE REV HI-CHROME |
485.0190-901 | VSI | T/CWP SET OUTER REV HI-CHROME |
485.0192-901 | VSI | T/CWP SET MIDDLE REV HI-CHROME |
485.0194-901 | VSI | T/CWP BOLT SET |
485.0195-901 | VSI | TOP WEAR PLATE SET |
485.0207-001 | VSI | ROTOR BOSS 690&760 |
485.0217-001 | VSI | FEED TUBE HOLDER |
485.0218-001 | VSI | 9600 CASCADE WEAR SKIRT KIT |
485.0223-001 | VSI | FEED TUBE CLAMP BLOCK |
485.0227-901 | VSI | T/CWP SET, NON REVERSIBLE |
485.0228-901 | VSI | BEARING CARTRIDGE **I-NOTE** |
485.0229-901 | VSI | BEARING CARTRIDGE **I-NOTE** |
485.0230-901 | VSI | BEARING CARTRIDGE **I-NOTE** |
485.0238-901 | VSI | 9600 CAVITY RING COARSE SET |
485.0239-901 | VSI | CAVITY RING ASSEMBLY 6900 |
485.0244-001 | VSI | FEED TUBE CLAMP SLEEVE |
485.0244-901 | VSI | DUOPACTOR CASCADE **SEE NOTE** |
485.0250-001 | VSI | SWING BOLT NUT *I-NOTE* |
485.0251-001 | VSI | ROOF SWING BOLT *I-NOTE* |
485.0251-501 | VSI | CAVITY RING 9600 - FINE |
485.0251-901 | VSI | SWING BOLT KIT *I-NOTE* |
485.0252-001 | VSI | SWING BOLT PIN *I-NOTE* |
485.0254-901 | VSI | BOLT ON GUSSET SET |
488.0029-001 | VSI | SPLIT TAPERLOCK MKIII 85HP&LP |
488.0040-901 | VSI | ROTOR ASSEMBLY LP85 |
488.0076-001 | VSI | CENTER DISTRIBUTOR PLATE |
488.0218-901 | VSI | ROTOR ASSEMBLY HP85 |
488.0258-001 | VSI | FEED TUBE |
488.0360-901 | VSI | UPPER WEAR PLATE SET |
488.0361-901 | VSI | LOWER WEAR PLATE SET |
488.0362-901 | VSI | TRAIL PLATE SET HP ROTOR |
488.0363-901 | VSI | CAVITY WEAR PLATE SET MID |
488.0364-901 | VSI | CAVITY WEAR PLATE SET TOP |
488.0365-901 | VSI | TRAIL PLATE SET LP ROTOR |
488.0366-901 | VSI | ROTOR TIP SET (SPLIT HARD) |
488.0367-901 | VSI | ROTOR TIP 1 PIECE SET (HARD) |
488.0368-901 | VSI | BACK UP TIP SET |
488.0369-901 | VSI | TOP WEAR PLATE SET HP ROTOR |
488.0372-901 | VSI | ROTOR BALANCING MACHINE |
488.0487-901 | VSI | CAVITY WEAR PLATE SET BOTTOM |
488.0488-901 | VSI | BRACKET |
488.0489-901 | VSI | KEY |
488.0501-901 | VSI | ROTOR BARE HP85 |
488.0502-901 | VSI | ROTOR BARE LP85 |
488.0694-901 | VSI | ROTOR BARE LP73 |
488.0721-001 | VSI | OUTER SPACING RING MKII BRG CARTRIDG |
488.0764-901 | VSI | ROTOR ASSEMBLY LP730 |
488.0769-001 | VSI | ROTOR TOP PLATE 73LP&EP |
488.0770-001 | VSI | CENTER DISTRIBUTOR PLATE |
488.0775-001 | VSI | SPLIT TAPERLOCK MKII 85HP&LP |
488.0793-001 | VSI | SPLIT ROTOR TAPERLOCK 73LP&EP |
488.0841-001 | VSI | ROTOR TOP PLATE 85HP&LP |
488.0842-901 | VSI | CNTR DIST LOCATING PIN&CAP SCREW SET |
488.0850-901 | VSI | UPPER WEAR PLATE SET |
488.0851-901 | VSI | LOWER WEAR PLATE SET |
488.0853-901 | VSI | TOP WEAR PLATE SET LP73 ROTOR |
841.0288-00 | VSI | DISTRIBUTOR PLATE BOLT |
500828-FR | HSI | SCREW |
501275-FR | HSI | NUT |
501286-FR | HSI | STRAP |
506461-FR | HSI | BEARING |
506470-FR | HSI | WITHDRAWAL SLEEVE |
506546-FR | HSI | BEARING |
506547-FR | HSI | WITHDRAWAL SLEEVE |
506548-FR | HSI | SPACER |
506549-FR | HSI | SLEEVE WITHDRAWAL |
506550-FR | HSI | BEARING |
506553-FR | HSI | SPACER |
506555-FR | HSI | BEARING |
506556-FR | HSI | WITHDRAWAL SLEEVE |
506557-FR | HSI | SPACER |
507936-FR | HSI | PIPE TEE ASSEMBLY |
508014-FR | HSI | CYLINDER BOOT |
508015-FR | HSI | CYLINDER BOOT |
508018-FR | HSI | HOOD |
508122-FR | HSI | HYDRAULIC CYLINDER |
508123-FR | HSI | HYDRAULIC CYLINDER |
508518-FR | HSI | LOCK WITH LATCH |
508519-FR | HSI | KEY FOR SAFETY DEVICE (FOR 508615-FR |
508615-FR | HSI | ELECTRO MECHANICAL LOCK |
508843-FR | HSI | HOSE |
532007-FR | HSI | HYDRAULIC CYLINDER |
700016-FR | HSI | SCREW |
700029-FR | HSI | SCREW |
700045-FR | HSI | SCREW |
700046-FR | HSI | SCREW |
700047-FR | HSI | SCREW |
700049-FR | HSI | SCREW FUNNEL LINER |
700051-FR | HSI | SCREW |
700052-FR | HSI | SCREW |
700088-FR | HSI | SCREW |
700100-FR | HSI | BOLT FOR 7200159-FR LINER |
700106-FR | HSI | SCREW |
700115-FR | HSI | SCREW |
700180-FR | HSI | SCREW |
700181-FR | HSI | SCREW |
700659-FR | HSI | SOCKET HEAD CAP SCREW **SEE I-NOTE** |
700904-FR | HSI | SCREW |
702014-FR | HSI | NUT |
702018-FR | HSI | NUT |
702020-FR | HSI | NUT |
702076-FR | HSI | NUT |
702307-FR | HSI | LOCKNUT |
702357-FR | HSI | LOCKNUT |
702362-FR | HSI | LOCKNUT |
702366-FR | HSI | LOCKNUT |
703012-FR | HSI | WASHER |
703084-FR | HSI | WASHER |
703086-FR | HSI | WASHER |
703093-FR | HSI | WASHER |
703110-FR | HSI | LOCKWASHER |
703208-FR | HSI | WASHER |
703213-FR | HSI | WASHER |
703255-FR | HSI | WASHER |
703256-FR | HSI | SPRING WASHER |
704021-FR | HSI | SPLIT PIN |
710003-FR | HSI | GREASE FITTING(SEE US710003-FR |
710627-FR | HSI | PLUG |
710801-FR | HSI | RING FOR BOOT |
710802-FR | HSI | RING |
710804-FR | HSI | RING FOR BOOT |
710806-FR | HSI | RING |
7200071-FR | HSI | DAMPER ASSEMBLY ( SEE ENG ) |
7200106-FR | HSI | HANGER |
7200109-FR | HSI | STOP PLATE |
7200115-FR | HSI | HYDRAULIC CYLINDER SUPPORT |
7200116-FR | HSI | THREAD PROTECTOR |
7200117-FR | HSI | PIVOT PIN |
7200118-FR | HSI | HAMMER MANG 45" |
7200120-FR | HSI | HAMMER CI 45" |
7200122-FR | HSI | HAMMER CS 45" |
7200124-FR | HSI | HAMMER MANG 30" |
7200126-FR | HSI | HAMMER CI 30" |
7200128-FR | HSI | HAMMER CS 30" |
7200133-FR | HSI | SHOCK ABSORBER |
7200138-FR | HSI | CHAIN FOR P300 |
7200142-FR | HSI | HOUSING COVER |
7200143-FR | HSI | COVER BEARING HOUSING |
7200144-FR | HSI | FLINGER |
7200145-FR | HSI | FLINGER |
7200146-FR | HSI | BEARING HOUSING |
7200147-FR | HSI | END SHAFT WASHER |
7200148-FR | HSI | SPACER |
7200150-FR | HSI | LINER ARS |
7200151-FR | HSI | LINER ARS |
7200152-FR | HSI | LINER |
7200155-FR | HSI | LINER |
7200158-FR | HSI | LINER |
7200159-FR | HSI | CURTAIN LINER ARS |
7200160-FR | HSI | WEDGE **see notes** |
7200163-FR | HSI | BEARING HOUSING |
7200164-FR | HSI | SPACER |
7200167-FR | HSI | BEARING HOUSING |
7200168-FR | HSI | HOUSING COVER |
7200169-FR | HSI | COVER BEARING HOUSING |
7200170-FR | HSI | FLINGER |
7200173-FR | HSI | FLINGER |
7200174-FR | HSI | SPACER |
7200197-FR | HSI | HANDLING TOOL |
7200198-FR | HSI | HEXAGON TOOL |
7200199-FR | HSI | OPEN HEX WRENCH |
7200200-FR | HSI | HANDLING BAR-45 INCH |
7200201-FR | HSI | HANDLING BAR-30 INCH |
7200208-FR | HSI | SPACER |
7200209-FR | HSI | LINER |
7200218-FR | HSI | LINER |
7200219-FR | HSI | LINER |
7200221-FR | HSI | LINER |
7200230-FR | HSI | LINER CHROME IRON |
7200231-FR | HSI | CURTAIN LINER-CS |
7200232-FR | HSI | SCREW |
7200234-FR | HSI | CHAIN ROD |
7200259-FR | HSI | LINER |
7200275-FR | HSI | LINER |
7200276-FR | HSI | LINER |
7200282-FR | HSI | FEED PLATE LINER |
7200285-FR | HSI | LINER |
7200286-FR | HSI | LINER ARS |
7200299-FR | HSI | TUDULAR CASING |
7200304-FR | HSI | FEED PLATE LINER |
7200306-FR | HSI | SPACER PLATE |
7200307-FR | HSI | SPACER PLATE |
7200318-FR | HSI | CLOSING PLATE |
7200321-FR | HSI | HOUSING |
7200326-FR | HSI | SIDE ANGLE |
7200327-FR | HSI | LOCKING ANGLE |
7200330-FR | HSI | STOP PLATE |
7200331-FR | HSI | DOOR |
7200341-FR | HSI | DOOR |
7200342-FR | HSI | DOOR |
7200343-FR | HSI | DOOR |
7200348-FR | HSI | CLOSING PLATE |
7200357-FR | HSI | LINER |
7200358-FR | HSI | HANGER |
7200368-FR | HSI | FEED PLATE LINER |
7200370-FR | HSI | THIRD CURTAIN |
7200371-FR | HSI | BEARING |
7200374-FR | HSI | CLOSING PLATE |
7200375-FR | HSI | CLOSING PLATE |
7200376-FR | HSI | DOOR |
7200377-FR | HSI | REAR DOOR |
7200378-FR | HSI | JOINT SUPPORT |
7200379-FR | HSI | COUNTER PLATE |
7200395-FR | HSI | DOOR |
7200397-FR | HSI | CLOSING PLATE |
7200398-FR | HSI | CLOSING PLATE |
7200407-FR | HSI | FEED PLATE LINER |
7200421-FR | HSI | LINER ARS FUNNEL |
7200423-FR | HSI | COVER |
7200434-FR | HSI | CURTAIN LINER MANGANESE |
7200445-FR | HSI | SCREW |
7200452-FR | HSI | TUBULAR CASING |
7200453-FR | HSI | SHOCK ABSORBER |
7200455-FR | HSI | BEARING |
7200456-FR | HSI | LIFT BEAM |
7200459-FR | HSI | STICKER |
7200472-FR | HSI | LINER |
7200507-FR | HSI | BEARING HOUSING |
7200508-FR | HSI | COVER BEARING HOUSING |
7200509-FR | HSI | FLINGER |
7200510-FR | HSI | FLINGER |
7200530-FR | HSI | NUT |
7200532-FR | HSI | HANGER |
7200690-FR | HSI | WEDGE |
7200693-FR | HSI | T-BOLT |
50512308-FR | HSI | FILTER ELEMENT |
50512309-FR | HSI | FILTER ELEMENT |
F1368997-FR | HSI | T-BOLT |
F1368998-FR | HSI | T-BOLT |
N7200104-FR | HSI | CONVERSION KIT-3 TO 2 CURTAIN*NOTES* |
N7200108-FR | HSI | CONVERSION KIT-3 TO 2 CURTAIN |
N7200109-FR | HSI | CONVERSION KIT-3-2 CURTAIN*I-NOTES* |
N7200110-FR | HSI | CONVERSION KIT-3 TO 2 CURTAIN |
N720031-FR | HSI | JIB CRANE KIT |
Metso OEM Model Table
OEM Number | Model | Description |
---|---|---|
1022061401/10 2206 1401 | HP200 | COUNTERSHAFT BUSHING |
1022061401-099 | HP200 | BUSHING CASTING |
1022130524 | HP200 | BUSHING |
1022072951/10 2207 2951 | HP200 | ECCENTRIC BUSHING, INNER |
1057602103/10 5760 2103 | HP200 | THRUST BEARING, UPPER |
1022072950/10 2207 2950 | HP200 | ECCENTRIC BUSHING |
1057602103-099 | HP200 | THRUST BEARING, ROUGH |
1048721001/10 4872 1001 | HP200 | SOCKET LINER |
1048721001-099 | HP200 | SOCKET LINER CASTING |
1022145719/10 2214 5719 | HP200 | HEAD BUSHING, UPPER |
1022145730/10 2214 5730 | HP200 | HEAD BUSHING, LOWER |
1022145719-099 | HP200 | BUSHING CASTING |
N55308011 | HP200 | MANTLE |
7055308001 | HP200 | MANTLE |
1050130815 | HP200 | MANTLE |
MM0376592 | HP200 | MANTLE |
N55308012 | HP200 | MANTLE |
7055308003 | HP200 | MANTLE |
7055308002 | HP200 | MANTLE |
MM0422414 | HP200 | MANTLE |
7055308006 | HP200 | MANTLE |
MM0422413 | HP200 | MANTLE |
N55208153 | HP200 | BOWL LINER |
7055208121 | HP200 | BOWL LINER |
MM0422415 | HP200 | BOWL LINER |
N55208135 | HP200 | BOWL LINER |
N55208136 | HP200 | BOWL LINER |
N55208138 | HP200 | BOWL LINER |
N55208139 | HP200 | BOWL LINER |
MM0403560 | HP200 | BOWL LINER |
N55208144 | HP200 | BOWL LINER |
N55208146 | HP200 | BOWL LINER |
N55208148 | HP200 | BOWL LINER |
N55208151 | HP200 | Bowl Liner Sh F |
N65558054 | HP200 | FEED CONE |
N55208156 | HP200 | BOWL LINER SPECIAL STD C |
N55308010 | HP200 | MANTLE SPECIAL STD F/M/C |
MM0422413 | HP200 | Mantle |
7084101513 | HP100 | REVEST. DO ASSENTO DA CARCAÇA,Frame seat liner |
7055208000 | HP100 | BOWL LINER |
7055208001 | HP100 | BOWL LINER |
7055308121 | HP100 | MANTLE |
7055308122 | HP100 | MANTLE |
MM0545036 | HP100 | BOWL LINER |
N65558006 | HP100 | FEED CONE |
1022061401/10 2206 1401 | HP300 | COUNTERSHAFT BUSHING, |
1022061401-099 | HP300 | BUSHING CASTING, |
1022130525 | HP300 | BUSHING |
1022073307/10 2207 3307 | HP300 | INNER ECCENTRIC BUSHING |
1057612200 | HP300 | UPPER THRUST BEARING |
7035800600 | HP300 | SOCKET LINER |
7015656200/70 1565 6200 | HP300 | UPPER HEAD BUSHING |
1022145975/10 2214 5975 | HP300 | LOWER HEAD BUSHING |
MM0368135 | HP300 | Mantle |
MM0374625 | HP300 | BOWL LINER |
MM0377272 | HP300 | BOWL LINER |
MM0403562 | HP300 | BOWL LINER |
MM0407650 | HP300 | Bowl Liner |
N55208279 | HP300 | BOWL LINER |
N55208280 | HP300 | BOWL LINER |
N55208281 | HP300 | BOWL LINER |
N55208282 | HP300 | BOWL LINER |
N55208283 | HP300 | BOWL LINER |
N55208284 | HP300 | BOWL LINER |
N55208285 | HP300 | BOWL LINER |
N55208286 | HP300 | BOWL LINER |
N55209126 | HP300 | BOWL LINER |
N55209127 | HP300 | BOWL LINER |
N55209128 | HP300 | BOWL LINER |
N55308265 | HP300 | MANTLE |
N55308266 | HP300 | MANTLE |
N55308267 | HP300 | MANTLE |
N55309124 | HP300 | MANTLE |
N55309125 | HP300 | MANTLE |
N55208275 | HP300 | Bowl Liner Sh M |
N55208272 | HP300 | Bowl Liner Std M |
N55308262 | HP300 | Mantle Sh/Std F/M/C |
MM0385332 | HP300 | MANTLE |
MM0423228 | HP300 | BOWL LINER |
N55308264 | HP300 | MANTLE |
N55208276 | HP300 | Bowl Liner Sh F |
N55208274 | HP300 | Bowl Liner Sh C |
N55208273 | HP300 | Bowl Liner Std F |
N55208271 | HP300 | Bowl Liner Std C |
N55209122 | HP300 | BOWL LINER M |
N55309121 | HP300 | MANTLE M/C |
1022133692 | HP4 | BUSHING,FOR EXTERNAL MAIN FRAME PINS, SEE INFO |
1022133692 | HP4 | BUSHING,FOR EXTERNAL MAIN FRAME PINS, SEE INFO |
1022133692 | HP400 | Main frame pin bushing |
1022062210/10 2206 2210 | HP400 | COUNTERSHAFT BUSHING |
1022074069/10 2207 4069 | HP400 | ECCENTRIC BUSHING |
1057605169/10 5760 5169 | HP400 | THRUST BEARING, UPPER |
N35800601 | HP400 | SOCKET LINER |
1022147349/10 2214 7349 | HP400 | HEAD BUSHING, UPPER |
1022147350/10 2214 7350 | HP400 | HEAD BUSHING, LOWER |
1048300035 | HP400 | BOWL LINER |
1048300039 | HP400 | BOWL LINER |
1048300043 | HP400 | BOWL LINER |
1066664407 | HP400 | BOWL LINER |
7055208382 | HP400 | BOWL LINER |
7055208392 | HP400 | BOWL LINER |
7055208395 | HP400 | BOWL LINER |
7055308381 | HP400 | MANTLE |
7055308387 | HP400 | MANTLE |
7055308388 | HP400 | MANTLE |
7055308389 | HP400 | MANTLE |
MM0297726 | HP400 | Mantle |
MM0342657 | HP400 | BOWL LINER |
MM0342658 | HP400 | MANTLE |
MM0377369 | HP400 | MANTLE |
MM0377370 | HP400 | BOWL LINER |
MM0401143 | HP400 | BOWL LINER SH EF |
MM0401145 | HP400 | MANTLE SH |
MM0403565 | HP400 | BOWL LINER |
MM0403568 | HP400 | BOWL LINER EF HP4 |
MM0403574 | HP400 | MANTLE |
MM0409187 | HP400 | MANTLE SPECIAL STD C |
MM0409189 | HP400 | BOWL LINER SPECIAL STD C |
N55208399 | HP400 | BOWL LINER |
N55208523 | HP400 | BOWL LINER |
N55208526 | HP400 | BOWL LINER |
N55209252 | HP400 | BOWL LINER |
N55209253 | HP400 | BOWL LINER |
N55209254 | HP400 | BOWL LINER |
N55209255 | HP400 | BOWL LINER |
N55209257 | HP400 | bowl liner fine |
N55209258 | HP400 | bowl liner |
N55309256 | HP400 | MANTLE |
N55309258 | HP400 | MANTLE |
N55309259 | HP400 | MANTLE |
N55309262 | HP400 | mantle fine |
N65558201 | HP400 | FEED PLATE |
N65558321 | HP400 | FEED CONE |
N98000008 | HP400 | FEED CONE |
MM0374621 | HP400 | Bowl liner |
MM0374622 | HP400 | Mantle |
MM0399538 | HP400 | MANTLE |
MM0399534 | HP400 | BOWL LINER |
MM0399536 | HP400 | mantle SH OS Med |
MM0399532 | HP400 | bowl liner SH OS Med |
7055308385 | HP400 | Mantle Sh F/M/C |
7055308384 | HP400 | Mantle Std F |
7055208394 | HP400 | Bowl Liner Sh M |
N55208527 | HP400 | Bowl Liner Std M |
N55208400 | HP400 | Bowl Liner Std C |
7055308380 | HP400 | MANTLE SPECIAL STD C |
7055208393 | HP400 | Bowl Liner Sh C |
7055208380 | HP400 | BOWL LINER SPECIAL STD C |
MM0364324 | HP400 | BOWL LINER |
7055208383 | HP400 | Bowl Liner Std F |
N55308512 | HP400 | Mantle |
1022139802 | HP500 | BUSHING |
1022065500/10 2206 5500 | HP500 | BUSHING |
1022074809/10 2207 4809 | HP500 | ECCENTRIC BUSHING |
1057605168/10 5760 5168 | HP500 | THRUST BEARING, UPPER |
1048723201/10 4872 3201 | HP500 | SOCKET LINER |
1022147321/10 2214 7321 | HP500 | HEAD BUSHING, UPPER |
N15655252/N 1565 5252 | HP500 | HEAD BUSHING, LOWER |
1048314241 | HP500 | BOWL LINER |
1048314242 | HP500 | BOWL LINER |
1048314243 | HP500 | BOWL LINER |
1048314244 | HP500 | BOWL LINER |
7055208515 | HP500 | BOWL LINER |
7055208520 | HP500 | BOWL LINER |
7055308501 | HP500 | MANTLE |
7055308509 | HP500 | MANTLE |
7055308510 | HP500 | MANTLE |
MM0396785 | HP500 | BOWL LINER |
MM0403527 | HP500 | BOWL LINER |
MM0403573 | HP500 | MANTLE |
N55308515 | HP500 | MANTLE |
N65558252 | HP500 | FEED PLATE |
MM0393814 | HP500 | BOWL LINER |
7055308503 | HP500 | Mantle Std F/M |
MM1074288 | HP500 | MANTLE |
MM1074284 | HP500 | BOWL LINER |
N55208532 | HP500 | BOWL LINER SH-C |
N55308520 | HP500 | MANTLE SH C OS |
MM0902821 | HP500 | Mantle (Fine) |
MM0902922 | HP500 | Bowl Liner (Fine) |
1022139802 | HP6 | BUSHING |
MM0395366 | HP600 | BOWL LINER |
MM0395367 | HP600 | MANTLE |
N55209500 | HP600 | BOWL LINER |
N55209502 | HP600 | BOWL LINER |
N55209503 | HP600 | BOWL LINER |
N55209504 | HP600 | BOWL LINER |
N55309501 | HP600 | MANTLE |
N55309502 | HP600 | MANTLE |
N55309508 | HP600 | MANTLE |
N55309509 | HP600 | MANTLE |
N55309511 | HP600 | MANTLE |
N65558322 | HP600 | FEED CONE |
MM0416859 | HP600 | MANTLE F OS |
MM0416861 | HP600 | BOWL LINER F OS |
MM0403570 | HP600 | Bowl liner |
MM0403577 | HP600 | Mantle |
MM0903523 | HP600 | MANTLE |
MM1090186 | HP600 | Mantle |
MM1090185 | HP600 | Bowl liner |
1048314350 | HP700 | Bowl Liner |
1048314345 | HP700 | BOWL LINER STD M |
1048314365 | HP800 | BOWL LINER |
1050143852 | HP800 | MANTLE |
1050143853 | HP800 | MANTLE |
MM0243062 | HP800 | MANTLE |
MM0350298 | HP800 | MANTLE |
MM0361734 | HP800 | FEED PLATE |
MM0394568 | HP800 | BOWL LINER |
MM0412732 | HP800 | Mantle |
MM0412733 | HP800 | Bowl liner |
MM0413496 | HP800 | bowl liner |
MM0413497 | HP800 | Mantle |
MM0355262 | HP800 | bowl liner |
MM1066906 | HP800 | MANTLE |
MM0419456 | HP800 | upper mantle |
MM0419457 | HP800 | lower mantle |
1050143811 | HP800 | Mantle |
1048314364 | HP800 | BOWL LINER |
1022075736/10 2207 5736 | MP1000 | Eccentric bushing |
1022148833/10 2214 8833 | MP1000 | Head bushing |
MM0344927 | MP1000 | Head bushing |
1022140676/10 2214 0676 | MP1000 | BUSHING |
1022070708/10 2207 0708 | MP1000 | COUNTERSHAFT BOX BUSHING |
1022075736/10 2207 5736 | MP1000 | ECCENTRIC BUSHING |
1057605258/10 5760 5258 | MP1000 | THRUST BEARING |
MM0344927 | MP1000 | HEAD BUSHING - UPPER |
1022148833/10 2214 8833 | MP1000 | HEAD BUSHING - LOWER |
11048727629 | MP1000 | |
1048315412 | MP1000 | BOWL LINER |
1048315551 | MP1000 | BOWL LINER |
1050144079 | MP1000 | MANTLE |
1050144088 | MP1000 | MANTLE |
10140645003 | MP1000 | MANTLE |
10140683003 | MP1000 | BOWL LINER |
33100010356003 | MP1000 | MANTLE UPPER |
MM0201016 | MP1000 | BOWL LINER |
MM0238373 | MP1000 | BOWL LINER |
MM0320744 | MP1000 | BOWL LINER |
MM0320745 | MP1000 | MANTLE |
MM0325413 | MP1000 | BOWL LINER |
MM0325416 | MP1000 | MANTLE |
MM0361801 | MP1000 | FEED PLATE |
MM0361807 | MP1000 | FEED PLATE |
MM0361814 | MP1000 | FEED PLATE |
1050144053 | MP1000 | Std C/M/F/EF MP1000 Mantle (stub shaft) |
MM0419957 | MP1000 | MANTLE, LOWER, STD EF |
MM0419952 | MP1000 | MANTLE, UPPER, SH F/M/C/EC |
MM0419923 | MP1000 | BOWL LINER, STD EF |
MM0428062 | MP1000 | FEED PLATE |
1022070708/10 2207 0708 | MP1250 | COUNTERSHAFT BOX BUSHING |
1022075736/10 2207 5736 | MP1250 | ECCENTRIC BUSHING |
1057605258/10 5760 5258 | MP1250 | THRUST BEARING |
1022148833/10 2214 8833 | MP1250 | HEAD BUSHING - LOWER |
MM0349235 | MP2500 | ECCENTRIC BUSHING |
1022147761/10 2214 7761 | MP800 | Lower head bushing |
1048724031/10 4872 4031 | MP800 | Socket liner |
1022075485/10 2207 5485 | MP800 | Eccentric Bushing |
1057610201 | MP800 | Thrust bearing |
1022140700/10 2214 0700 | MP800 | BUSHING |
1022066796/10 2206 6796 | MP800 | COUNTERSHAFT BOX BUSHING |
1022075485/10 2207 5485 | MP800 | ECCENTRIC BUSHING |
1057610201 | MP800 | THRUST BEARING (UPPER) |
1048724031/10 4872 4031 | MP800 | SOCKET LINER |
1022147761/10 2214 7761 | MP800 | HEAD BUSHING (LOWER) |
1048315201 | MP800 | BOWL LINER |
1048315202 | MP800 | BOWL LINER |
1048315255 | MP800 | BOWL LINER |
1050143900 | MP800 | MANTLE |
1050143953 | MP800 | MANTLE |
MM0212546 | MP800 | BOWL LINER |
MM0299682 | MP800 | BOWL LINER,SH M OS |
MM0314033 | MP800 | BOWL LINER |
MM0325415 | MP800 | BOWL LINER |
MM0325417 | MP800 | MANTLE |
MM0356892 | MP800 | MANTLE |
MM0361751 | MP800 | FEED PLATE |
MM0404949 | MP800 | MANTLE,SPECIAL SH OS |
MM0405104 | MP800 | BOWL LINER |
MM0407554 | MP800 | MANTLE |
MM0410484 | MP800 | MANTLE |
MM0410485 | MP800 | BOWL LINER |
MM0416219 | MP800 | BOWL LINER |
MM0416220 | MP800 | MANTLE |
MM0422425 | MP800 | Bowl liner |
MM0404948 | MP800 | MANTLE,SPECIAL SH OS |
MM0411641 | MP800 | Bowl liner |
MM0396432 | MP800 | BOWL LINER,SH M |
MM0357846 | MP800 | MANTLE |
949628506200 | GP100 | FRAME BUSHING,G800-SARJA 285062, |
285063 | GP100 | RING |
171565 | GP100 | BEARING BUSHING,E16 G158, |
171551 | GP100 | BEARING BUSHING,E20 G158, |
171564 | GP100 | BEARING BUSHING,E25 G158, |
814317178300 | GP100 | CONCAVE |
814317183600 | GP100 | CONCAVE |
814318865500 | GP100 | CONCAVE |
814328537700 | GP100 | CONCAVE |
814328537800 | GP100 | MANTLE |
MM0309236 | GP100 | MANTLE |
949617145500 | GP100S | Eccentric Bush G258 20mm Throw |
949628506200 | GP100S | FRAME BUSHING |
949628506400 | GP100S | SUPPORT BUSHING |
949617145700 | GP100S | BEARING BUSHING |
949617145600 | GP100S | Eccentric Bush G258 20mm Throw |
814317177900 | GP100S | MANTLE |
814328570600 | GP100S | CONCAVE, LOWER |
814329234600 | GP100S | CONCAVE, UPPER |
941534 | GP11 | THRUST BEARING,PALIER DE BUTEE,LAGER |
949620310900 | GP11 | FRAME BEARING , MM0315148 |
285417 | GP11 | BEARING BUSHING, |
285344 | GP11 | Eccentric BUSHING, |
285385 | GP11 | BEARING BUSHING, |
MM0273426 | GP11 | Eccentric BUSHING |
MM0315148 | GP11 | Frame bearing bushing, 949620310900 |
814317169500 | GP11F | MANTLE |
814317171900 | GP11F | CONCAVE |
814317177700 | GP11F | CONCAVE |
814320044100 | GP11F | MANTLE |
814390827200 | GP11F | MANTLE |
814318848600 | GP11M | MANTLE |
814318848700 | GP11M | CONCAVE |
814390523400 | GP11M | CONCAVE |
941535 | GP200 | THRUST BEARING Set |
942951 | GP200 | 机架铜套,FRAME BUSHING |
933617 | GP200 | Eccentric bushing |
MM0524454 | GP200 | |
N11933947 | GP200 | MANTLE |
N11933949 | GP200 | CONCAVE |
N11942003 | GP200 | MANTLE |
N11942004 | GP200 | CONCAVE |
N11944214 | GP200 | CONCAVE |
N11944215 | GP200 | CONCAVE |
908527 | GP200S | ECCENTRIC BUSHING,GP200S 18/25/32 |
941535 | GP200S | THRUST BEARING,GP200S |
942951 | GP200S | FRAME BUSHING |
MM0524454 | GP200S | |
814390727700 | GP200S | MANTLE |
814390727800 | GP200S | CONCAVE |
814390727900 | GP200S | CONCAVE, UPPER |
814391704400 | GP200S | CONCAVE,LOWER |
MM0236637 | GP200S | CONCAVE, LOWER |
N11950100 | GP200S | MANTLE |
MM0236637 | GP200S | CONCAVE, LOWER |
N11950100 | GP200S | MANTLE |
MM1102104 | GP220 | |
MM0528576 | GP220 | MANTLE |
MM0528578 | GP220 | CONCAVE |
MM0542797 | GP220 | CONCAVE F/MF |
MM0542884 | GP220 | MANTLE EF/F |
MM0542955 | GP220 | MANTLE M/C/EC-LS |
MM0554568 | GP220 | CONCAVE M |
MM0566674 | GP220 | MANTLE MF/M/C/EC OS |
MM0581249 | GP220 | CONCAVE C |
MM0592982 | GP220 | CONCAVE EF |
MM1000278 | GP220 | CONCAVE EC-LS |
MM1088414 | GP220 | Concave |
MM1088407 | GP220 | Mantle |
MM0537909 | GP250 | |
MM0227358 | GP300 | ECCENTRIC BUSHING 28/36 |
938379 | GP300 | THRUST BEARING SET |
931714 | GP300 | FRAME BUSHING |
MM0266967 | GP300 | Eccentric bushing 25/32/40 |
292723 | GP300 | |
814318940300 | GP300 | MANTLE |
814390455800 | GP300 | CONCAVE |
N11905094 | GP300 | CONCAVE |
N11920192 | GP300 | MANTLE |
N11920194 | GP300 | CONCAVE |
N11920195 | GP300 | CONCAVE |
N11920196 | GP300 | MANTLE |
N11920197 | GP300 | CONCAVE |
MM0205078 | GP300 | Concave |
MM0521380 | GP300/S | |
MM0523930 | GP300/S | |
MM0244630 | GP300S | Eccentric bushing |
MM0227940 | GP300S | Eccentric bushing |
938379 | GP300S | THRUST BEARING |
931714 | GP300S | BEARING |
MM0315854 | GP300S | Eccentric bushing |
188325 | GP300S | Eccentric bushing,18/25/32/40 |
MM0315834 | GP300S | Eccentric Bushing 18/25/32 |
814318836900 | GP300S | MANTLE |
814318862000 | GP300S | CONCAVE |
814390336100 | GP300S | MANTLE |
814390336200 | GP300S | CONCAVE |
MM0288155 | GP300S | Concave |
N11945881 | GP300S | Mantle |
N11947566 | GP300S | Concave |
189611 | GP500S | PROTECTION PLATE |
189612 | GP500S | PROTECTION PLATE |
N11941327 | GP500S | MANTLE |
N11947962 | GP500S | CONCAVE |
N11951712 | GP550 | MANTLE |
N11951715 | GP550 | CONCAVE |
N11951717 | GP550 | CONCAVE |
N11951716 | GP550 | Concave |
N11951713 | GP550 | Concave |
N11951714 | GP550 | Concave |
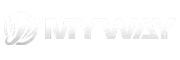
Zhejiang Myway Co., Ltd. was established in 2005 and has grown into a leading company in the bushing industry. It has more than 20 years of experience in high-quality bushing research, development and production.
Copyright © 2025 Zhejiang Myway Co., Ltd. All Rights Reserved.
Quick Links
Address
Greenland Central Plaza, Gongshu District, Hangzhou City, Zhejiang Province, China