Is a Sleeve Bearing Better Than a Ball Bearing?
Table of Contents
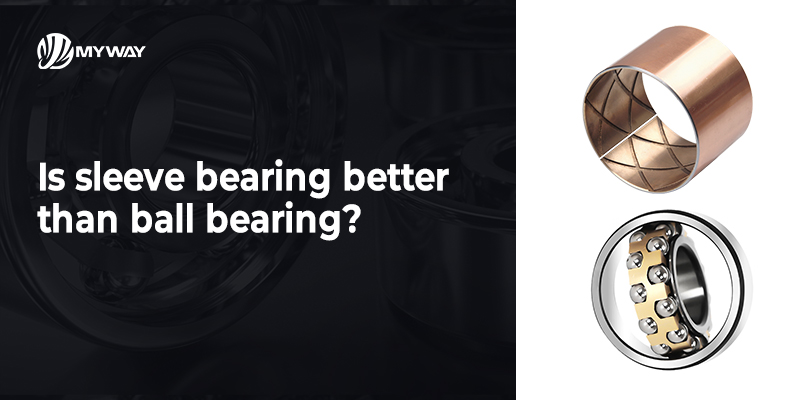
Is a sleeve bearing better than a ball bearing? Well, it depends on your situation and the operating environment you have. Each has its best uses and also it’s not-so-best uses. We’re going to get into an in-depth comparison of the two and answer the questions how to tell if your motor is sleeve or ball bearing and what is the difference between a sleeve bearing and a rolling bearing in detail.
For more information about how we apply the one or the other, read our related article “Bushings vs Bearings: Application Differences.”
Is a bearing and a bushing the same?
What is a Sleeve Bearing?
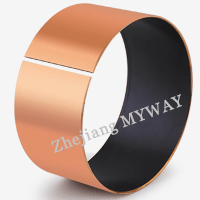
A big word for sleeve bearing is plain bearing. This is simply a piece of a tube that you use in between the shaft that is rotating and whatever the shaft is rotating in by using sliding friction. You would use a plain bearing in an application where the load and speed are light to moderate.
Advantages of Sleeve Bearings:
Disadvantages of Sleeve Bearings:
What is a Ball Bearing?
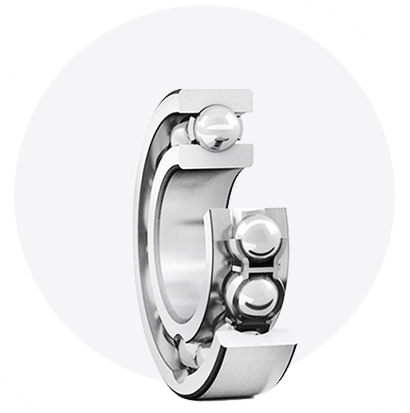
A ball bearing is a “rolling-element bearing” that uses balls to reduce friction between moving parts. The balls rotate between the inner and outer races, decreasing friction because the balls only touch the inner and outer races in a very small spot.
Advantages of Ball Bearings:
Disadvantages of Ball Bearings:
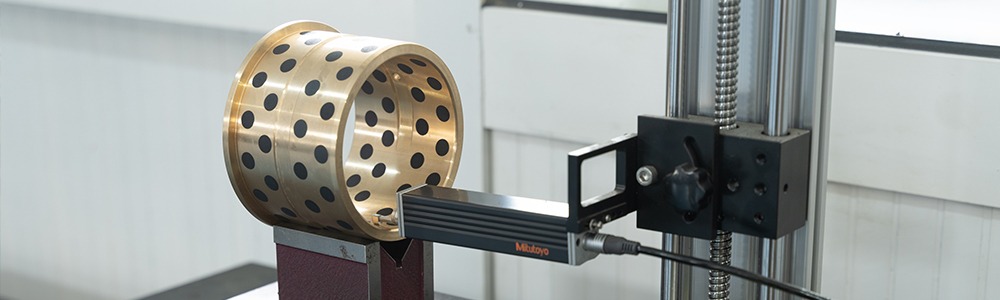
How Do I Know If My Motor Is Sleeve or Ball Bearing?
1. Read the Specifications
Check out your motor’s data plate, your manuals, manufacturer specifications, and so on. Generally, they will disclose somewhere in the documentation if they are using ball bearings or sleeve bearings in the motor.
2. Noise (Sound)
Sleeve bearings run more quietly because they are based on sliding friction.
Ball bearings run noisier, especially at high speeds because those little balls in there are what make the noise.
3. Speed
If your motor is running at a high speed, the chances are pretty good it’s using ball bearings.
4. Maintenance Requirements
Most self-lubricating motors are sleeve bearings. Ball bearings typically require grease or oil to be reapplied periodically.
5. Can you take it apart and inspect it?
If you have your motor on the bench (and you can do this with it), take it out and place it on a workbench. Then remove the housing and see if the bearing is visible.
What is the Difference Between a Sleeve Bearing and a Rolling Bearing?
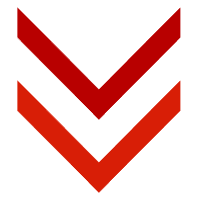
Then we have sleeve bearings and rolling element bearings. We’re dividing up how you handle that friction and how it allows things to move or not move.
Key Differences:
Feature | Sleeve Bearing | Rolling Bearing (Ball or Roller) |
Friction Mechanism | Relies on sliding friction. | Relies on rolling friction using balls or rollers. |
Load Capacity | Handles moderate loads. | Handles higher loads, both radial and axial. |
Speed Capability | Best for low to moderate speeds. | Suitable for high-speed applications. |
Noise | Operates quietly due to lack of rolling elements. | Produces more noise, especially at high speeds. |
Maintenance | Self-lubricating options require less maintenance. | Requires periodic lubrication for optimal performance. |
Durability | Performs well under consistent low-speed conditions. | Handles heavy loads and frequent directional changes. |
Cost | Lower cost due to simpler design. | Higher cost due to complex manufacturing. |
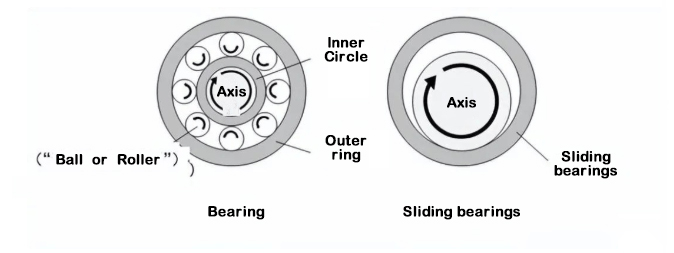
Sleeve Bearing vs. Ball Bearing: Which Is Better?
The answer depends on your application requirements. Below is a quick comparison:
Feature | Sleeve Bearing | Ball Bearing |
Best For | Low-speed, low-load, quiet operations. | High-speed, high-load, precision operations. |
Noise | Quiet operation. | Noisier operation. |
Cost | Cost-effective and affordable. | More expensive. |
Speed Limitation | Not suitable for high speeds. | Ideal for high-speed applications. |
Load Capability | Handles moderate radial loads. | Handles both high radial and axial loads. |
Maintenance | Low maintenance, especially with self-lubricating designs. | Requires regular lubrication. |
Conclusion
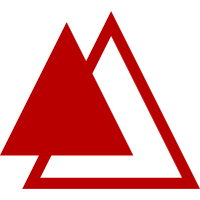