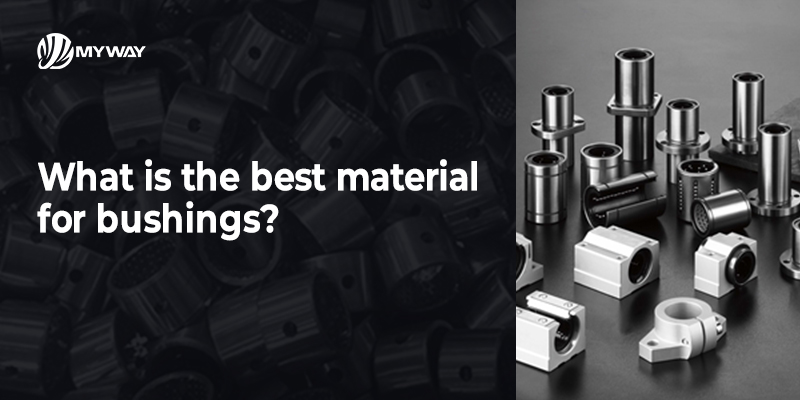
The material is very important when choosing bushings for your machinery. The material you choose can make a big difference in how well your equipment functions, how long your bushings last, how broken down your machinery is and how well it produces for you. The ideal material depends on the particular application, load conditions, temperature, and whether they must operate in wet or other harsh conditions. I can help you choose the best material for your application. Here are some materials we provide and what they do and do not do for you.
Table of Contents
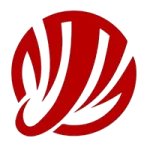
What are Bushings and What do They Do?
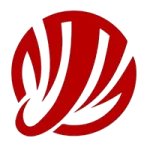
What are the Most Common Materials for Bushings?
When it comes to making bushings, (many) materials can be used to make the bushings, so different materials offer different pluses and minuses. Here are the top materials to consider:
Bronze
- Advantages: Bronze bushing is considered a very top choice for anything because of its wear resistance, satisfied with the high loads, low friction, and it can handle the heat. So the bronze bushing is very durable.
- Applications: Automotive, marine, industrial machinery, and mining equipment.
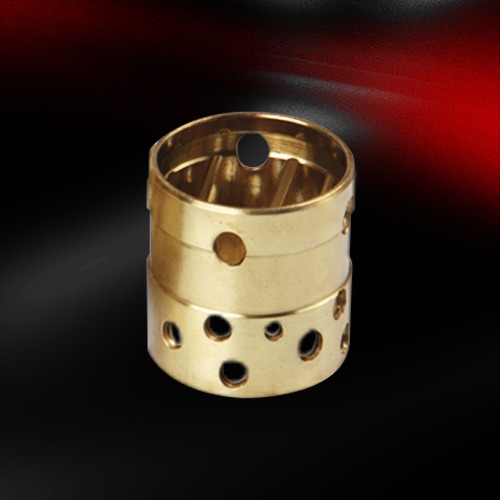
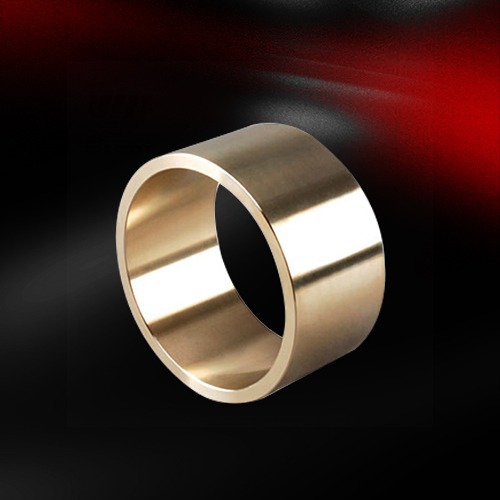
Steel
- Advantages: Steel bushings are tough, durable, and their cost compared to bronze makes them friendly on the pocketbook. Steel works well for high load applications. Steel also can be heat treated to get a lot more wear resistance and hardness. Steel is good for applications where there’s very little lubrication.
- Applications: Automotive, construction machinery, industrial equipment.
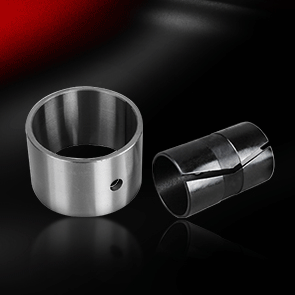
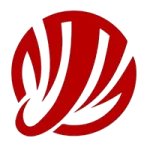
Composite Materials (Plastic&Metal Composites)
- Advantages:That would be a composite bushing. They combine plastic materials (like teflon, PEEK or nylon) with a metal bushing, resulting in a bushing that’s very resistant to wear. It can handle a lot of chemical corrosion, and it can handle high temperatures. They’re lightweight and self-lubricating, therefore you don’t have to provide external lubrication.
- Applications: Aerospace, automotive, food processing, and pharmaceutical machinery.
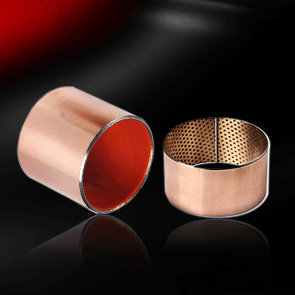
Nylon (Polyamide)
- Advantages: Nylon bushings are very lightweight. They wear like iron, they are self-lubricating, they hold up their own lubrication well, they are impervious to almost all forms of chemical attack, and they are great for anything from moderate to low load.
- Applications: Automotive, consumer goods, agricultural machinery, and low-load industrial applications.
Polyurethane
- Advantages: Polyurethane bushings are very flexible and very good with impacts and abrasions. Many times they are in environments where you need them to absorb impacts. Polyurethane bushings are very good with oils, greases, and water.
- Applications: Suspension systems, automotive, mining, and material handling equipment.
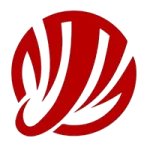
How Do You Choose the Best Material for Bushings?
Deciding which is the best material for your bushings depends on specific characteristics of your application. Here are some things to keep in mind as you look at the different materials.
- Load and Stress: For heavy load applications, use bronze, steel, or composite materials. The bronze will hold up well. Steel will get you steel bearings, and composite material is durable and doesn’t wear under stress.
- Speed and friction: If you need the bushing to run super fast at higher speeds, then people go to materials like bronze, copper and composite materials like PTFE that have very low friction properties.
- Temperature: If you need the bushing in a high-heat type of situation people use bronze, copper and composite materials. If you need a bushing that can do pretty good at low or average temperatures or stand up better to hotter temperatures than a nylon or plastic bushing you would use bronze, copper and composite materials.
- Corrosion Resistance: For wet, chemical, or salt applications, materials like bronze, copper, composites resist corrosion better than steel, or inexpensive plastics.
- Lubrication Needs: If you can’t put a lot of lubrication on your part, use a material like bronze, certain composite materials, or self-lubricating plastics like PTFE or PEEK that do a good job of reducing friction even without external lubrication.
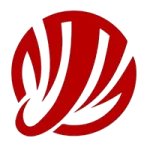
What Are the Advantages of Self-Lubricating Bushings?
Benefits:
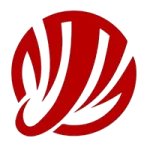