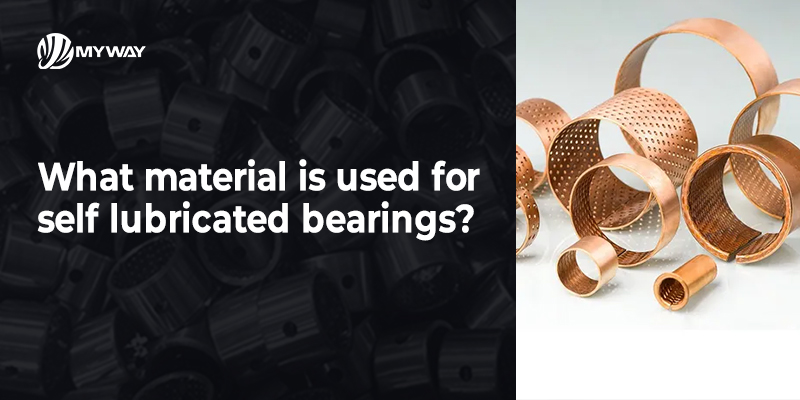
Self-lubricated bearings are made to reduce friction, wear and need for external lubrication. This makes them perfect for situations where lubrication would be difficult, where lubrication is impractical, where maintenance is limited, and where space in the application doesn’t allow for a lubrication method. Why are they so awesome? What makes them work so well? The answer is in the material used to create the bearing.
“Let’s talk first in this article about the different materials used to make these self-lubricated bearings, where you would use them and why. What makes them a superior choice in your industrial application?”
Table of Contents
1. Composite bushing (SF-1, SF-2)
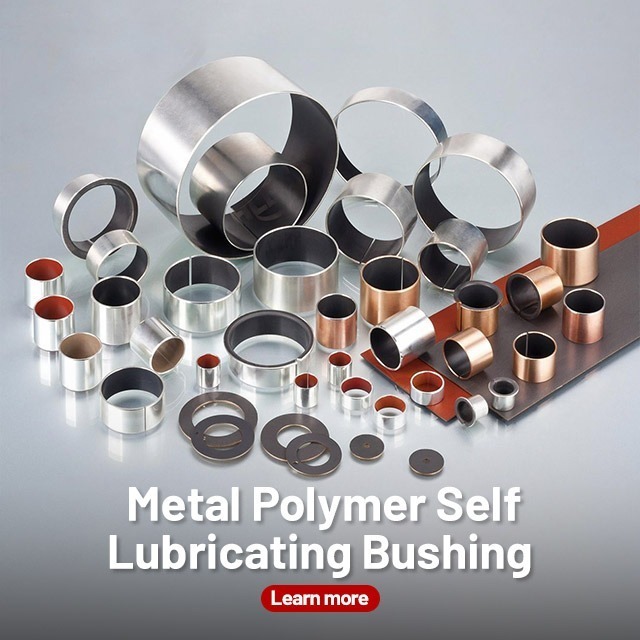
There’s also something else called a composite bushing. It’s a liner made up of multiple liners, typically metal, plastic, and some other high-performance materials. It’s typically used in mechanical engineering and the car business to reduce friction and reduce wear and corrosion. Generally, composites take WAY more load, work in higher heat, and work in more abrasive environments giving better performance and much longer life.
2. Bimetallic Bushing
A Bimetallic self-lubricated Bushing is designed with two different metals typically two layers. Bushing made with a steel or tough material on the outside and often a softer metal like bronze or copper on the inside that gives it great durability as well as self-lubrication.
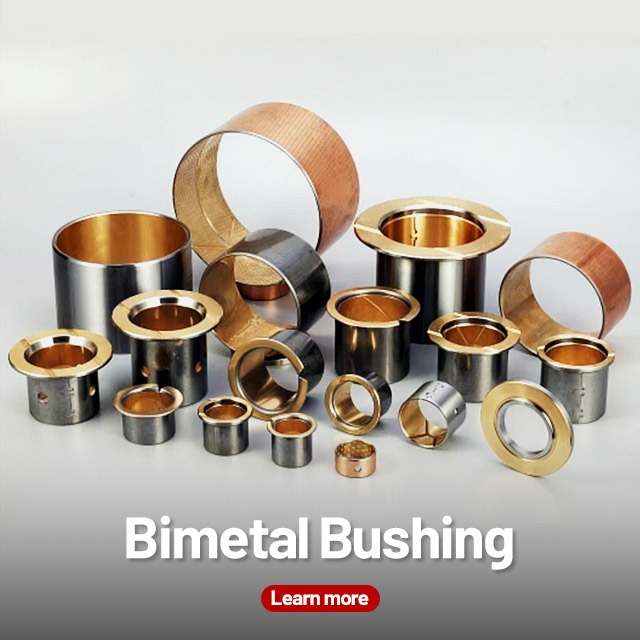
3. Graphite-Embedded Materials
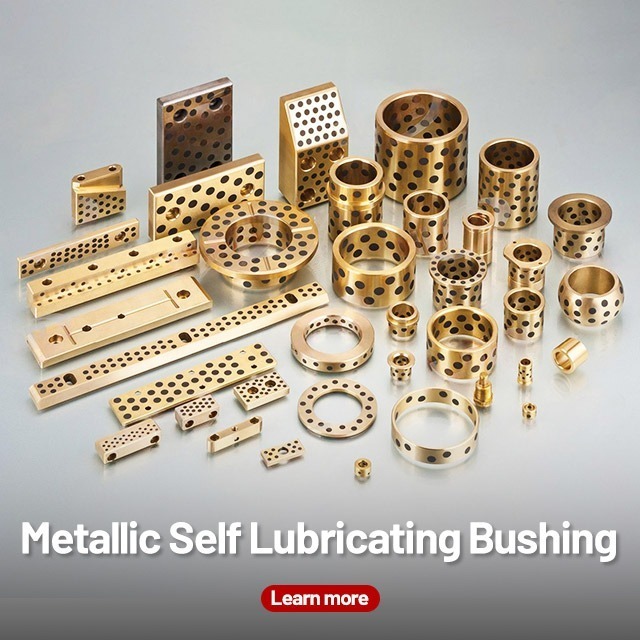
Graphite is used the most frequently as a solid lubricant. It has very good anti-friction characteristics and a high-temperature tolerance. A favorite application is a bushing, which can be made with a matrix that contains embedded graphite particles, incredible combination to use in severe environments where extreme loads and temperatures are present.
4. Copper-Based Alloys
For self-lubricating bearings, one good place to use copper or a copper-based alloy (copper tin or copper zinc) is because copper doesn’t corrode very well, and it has great thermal conductivity. These can also impregnate these same materials with a solid lubricant, graphite or PTFE or another type of solid lubricant.
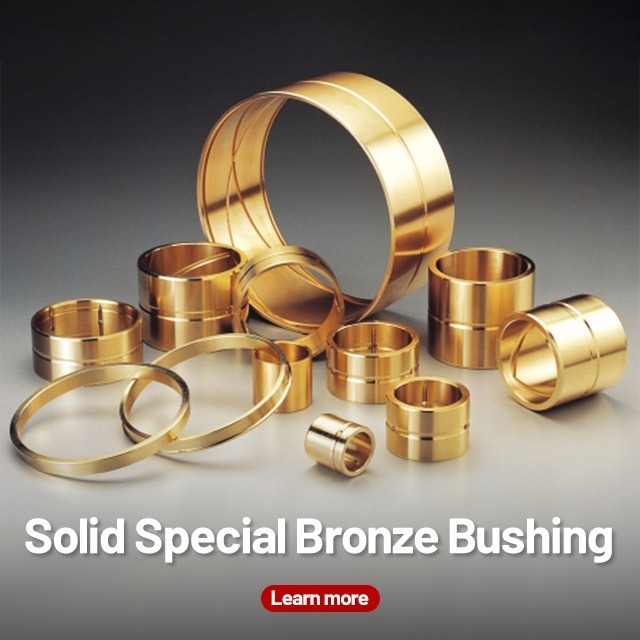
5. Powder Metallurgy Bushing
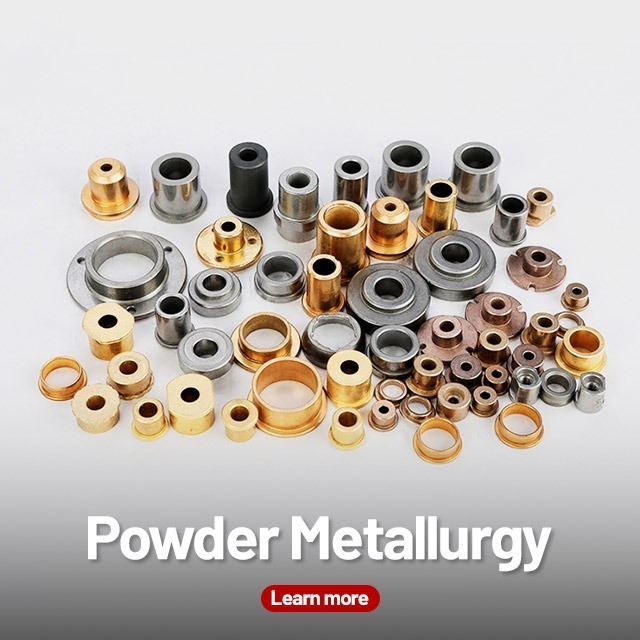
Powdered metal technology is where metal powders are mixed with lubricants like graphite or MoS₂, then compressed into the shape of a bushing. By forming it this way, you end up with a porous structure that holds the liquid within the material to provide constant self-lubrication.